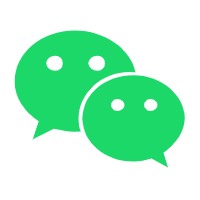
自2008年全球金融海啸导致各欧美传统强国经济重创、欧债危机爆发,各国政府近年来开始将制造业竞争力列为重点目标,促使各国政府重新重视制造业的重要性,如2011年德国提出「工业4.0」,主要着重在推动「 智能工厂」,发展许多技术策略,如自动化机器人、大数据数据分析、物联网、网络服务等,以人机共同合作模式来提升产品生产力及质量管理。 藉此除了提高不少生产价值外,更能维持在全球制造领域的领先优势。
本文主要以3D影像视觉为基础,检测轮胎缺陷为例,首先了解自动光学检测(Automated Optical Inspection, AOI)技术及其重要性,再说明AOI技术导入缺陷检测取代传统人力目视检测, 最后利用3D视觉缺陷检测技术结合实际应用,于不同类型产品进行缺陷检测。
改进传统目视检测缺点 自动光学检测精确度高
自动光学检测或自动表面检测(Automated Surface Inspection, ASI)主要以「机器视觉」做为检测关键技术,利用高精确度、高速度的光学仪器,以非接触的方式取得产品的外观表面状态, 接着再以图像处理技术取代人类肉眼来检测出是否有无异物或异常裂痕等瑕疵,改进传统上以人力目视进行检测的缺点,细微缺陷误差较不易察觉等问题。
AOI技术导入好处多 产品不良率大减
AOI应用领域非常广泛,包含量测镜头技术、光学照明技术、定位量测技术、电子电路测试技术、图像处理技术及自动化技术应用等领域,广义的AOI设备为结合光学感测系统、讯号处理系统及分析软件,应用层面可包括宇宙探测、航空、 卫星遥测、生物医学、工业生产质量检测、指纹比对、机器人控制、多媒体技术。 应用产业包括了食品加工、建筑、电子、机械、钢铁、轮胎、纺织及半导体等。
应用于工业检测技术方面,相关设备大厂如ISRA Parsytec、康耐视(Cognex)、LASE、SmartRay等,也逐渐开始将3D视觉核心技术投入研发,突破过去主流基于亮度的图像处理技术,有效提升缺陷检测的准确性, 3D影像之表面缺陷检测技术为一个新颖且值得去深入研究的领域,若未来能稳定成熟发展此项技术,将带给工业检测技术另一个高峰。
自动光学检测技术是一种自动化的机器视觉检测技术,对于提升产能与产品质量扮演着相当重要的角色,取代传统的人工目视检测,应用层面广泛。
近年来,世界各国纷纷投入3D可视化技术实际应用,藉此突破过去基于亮度之影像技术,常受限于作业现场环境光线、机器设备或制造材质等影响,检查工程时容易导致肉眼判断失准,不注意就会遗漏缺陷或瑕疵, 无法准确侦测或辨识出问题所在位置,在所有产品制造阶段,缺陷检测是非常重要的一环,为产品的质量做最后把关,有好的质量才能持续赢得消费者的信赖。
自动光学检测结合几个重要的架构,光学照明部分,透过CCD镜头(Charge Coupled Device)(图1)、光学照明设备,将光学图像转换为电子讯号;系统主机部分,由PC与周边组成;动力控制部分,可程序逻辑控制器( PLC)或PC Base控制主机;图像处理部分,图像处理算法、软件、通讯设备等。
图1 CCD自动光学镜头处理检测对象
数据源:wikipedia[1]
在进行工业自动化生产过程中,由于传统产品检测大多是以人力为主,不仅生产率有限,消耗的人事成本也相对较高,也会有人为误判的机率。 而AOI技术投入在产品自动化制程中,除了能大幅缩短检测缺陷时间、降低产品不良率、准确检测出人类目视所遗漏的缺陷与异物等,稳定度和生产效率也会有显著的成长。
随着机器视觉技术不断进步与成长,应用领域也越来越广泛,像是在工业检测与商业应用方面,机器视觉技术常被用来检测产品瑕疵缺陷部分,此技术本身具有成本低、效率高、准确度佳等优点,是人机互动中关键技术之一。
用机器视觉技术结合自动化检验制程中工业产品之瑕疵,能提高整体制程效能,如电路板线路上之缺陷、半导体晶圆外观表面检测裂痕缺陷、LCD面板表面之缺陷瑕疵等肉眼较不易检测的缺陷,皆能使用自动化缺陷检测技术达到产能提升、质量稳定 、降低生产成本、减少人为误差等效益。
自动化缺陷检测应用于产品实例,元智大学工业工程与管理学系之机器视觉实验室建立一套自动化的检测系统,于太阳能硅芯片(Solar Wafer)之微裂瑕疵检测。 太阳能硅芯片具有复杂晶格纹路之特性,因此利用非线性扩散(Anisotropic Diffusion)设计一个扩散系数函数,同时使用灰阶值与灰阶梯度值做为扩散处理的权重因子,将改善后的非线性扩散模式, 将针对瑕疵区域进行较大程度的扩散平滑处理,并且抑制正常表面区块的平滑效果。
藉由改善后的非线性扩散模式将太阳能芯片正常区块之灰阶保留不变且针对微裂瑕疵之灰阶做平滑处理,接着使用原始影像与经过扩散处理结果之影像相减,以去除正常区块并凸显微裂瑕疵于差异影像(Difference image)中, 最后使用二值化与形态学(Morphology)后处理技术分割瑕疵并去除噪声。
图2显示太阳能芯片具有复杂纹路特性以及微裂瑕疵,肉眼不易察觉,必须经由机器视觉技术处理后,可成功去除复杂的背景纹路以及找到微裂瑕疵之正确位置。
图2 (左)太阳能芯片微裂瑕疵影像(右)检测结果
数据源:元智电子报-机器视觉研究与相关应用,工业工程与管理学系所-蔡笃铭教授[2]
增进AOI技术效率 3D可视化技术达阵
目前许多AOI技术是基于亮度为主流,依赖作业现场环境光源、设备、材质等因素限制,检测缺陷之准确率无法维持稳定,容易遗漏缺陷产品等问题。 因此,本文提出以3D可视化缺陷检测技术应用于轮胎产品,自动化扫描轮胎表面状态,3D可视化方式来呈现整体轮胎表面深度纹理,导入范围影像技术达到缺陷检测之目标。
目前市面上常见的3D扫描技术主要分为接触式和非接触式技术,接触式量测技术经由探针接触待测物体取得相关信息回传至计算机,大多利用在大型对象检测,非接触式量测技术,也可称做3D扫描,透过光学镜头组, 搭配雷射光或不同光源投射的变化,取得对象的反射加以分析成为数字信息。
取得轮胎表面3D影像 缺陷检测时间大缩短
3D非接触式扫描的应用以SmartRay ECCO 75.100为例,SmartRay ECCO 75.100具有高扫描速率,其内装的摄影机与雷射光源采三角量测法的原理来设置,藉由SmartRay ECCO 75.100的雷射光源打在待测物体表面上,由内建摄影机镜头接收反射光,能实时取得物体表面形状之完整的3D点云信息,以利后续处理与分析。 待测物体表面上有残余异物或裂痕缺陷等问题能够轻易被观察,以利往后经由图像处理技术自动回报缺陷部分,提高缺陷检测准确率(图3)。
图3 (左)SmartRay ECCO 75.100(右)测量范围示意图
数据源:SmartRay官方网站[3]
SmartRay ECCO 75.100向待测物体投射出光线后,由内嵌摄影机接收坐标数据取得3D点云信息,图4是将光学扫描后取得的点云信息,绘制出3D轮胎缺陷影像,不同颜色变化对应于深度值高低,缺陷区块色彩差异较显著, 利用机器视觉技术可轻易辨识、撷取细微缺陷部分,提升缺陷辨识准确度。
图4 依色彩区分深度值之3D轮胎缺陷影像
传统轮胎检测是以人力进行为主,为了检测大量轮胎常常得耗费相当大量的人力资源与时间成本,且人工目视检测也可能有误差,而基于3D视觉为基础的轮胎缺陷检测技术可以针对轮胎表面进行扫描检测,取得其表面3D范围影像,缺陷、 异物或瑕疵等部分能被轻易观察,取代人工检测产品的问题,大幅缩短检测时间,如此一来,不仅降低人力成本,同时也能稳定提升生产效率。
本文案例中,雷射光学仪器打出一直线激光束,透过激光束对轮胎表面样本作整体扫描,能及时取得轮胎表面形状之3D点云信息,利用各种图像处理方法将不需要的部分滤除,留下影像特征透过瑕疵检测算法来辨识、分类。 以色彩变化对应于深度信息,可视化呈现缺陷部分之差异,以利后续图像处理快速找出缺陷部分。
由于轮胎材质较为特殊,且大多数轮胎表面颜色呈现黝黑色,对光线投射于表面反射出来的亮度变化较不明显,导致传统基于亮度为基础的图像处理技术应用于轮胎检测效果不佳,3D点云信息不受限于环境光线、产品材质等影响, 自动呈现3D深度影像。
轮胎制程进入最后阶段,将会进行严格的质量把关检测,轮胎质量高低取决于轮胎整体是否有无裂痕、胎内外异物残留、气泡缺陷等问题,且每条轮胎缺陷状况不一,必须判断是否符合质量规范标准,若符合标准才能出厂(图5)。
图5 轮胎制程流程图
数据源:痞客邦-走过必留下痕迹,陈妤瑄重制(11/2017)
轮胎缺陷检测应用方面,从轮胎表面的检测技术,除了可用于生产制造过程中的全面性的质量检测之外,亦可运用于车辆维修保养之定期或不定期的检测,保障轮胎使用期间的行车安全。
产品自动化制程中,产品质量控管与检验是最后且非常重要的步骤,除了掌握缺陷瑕疵部分,也要减少生产成本,才能达到最大效益。
3D可视化缺陷检测(图6)是一门新兴的专业技术,取代传统人工检测、大幅缩短检测时间、人为误差、克服环境光源不足等多种缺点,不仅加速产品研发速度,同时也能降低产品不良率,创造产品价值,提升产业未来的发展性。
图6 3D可视化缺陷检测流程图
(本文作者任职于资策会智通所)
暂无评论哦,快来评论一下吧!
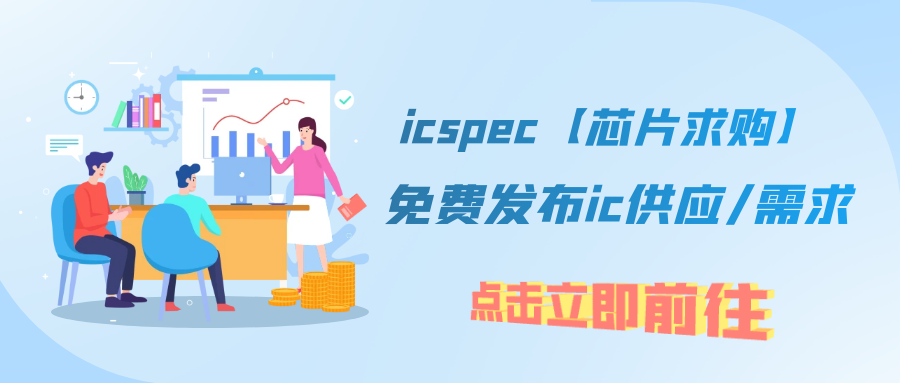
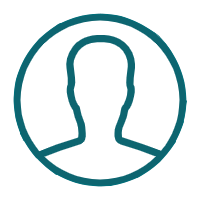