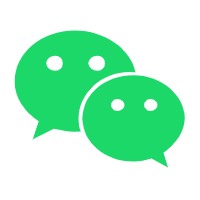
关注公众号,点击公众号主页右上角“ · · · ”,设置星标,实时关注功率半导体生态圈最新资讯
来源:思瀚产业研究院
(1)行业概况
1)产品概述
良好的热管理对于功率模块稳定性和可靠性尤为重要,相较于其他应用领域,新能源汽车电机控制器用功率半导体模块面临着更为复杂的使用环境和特殊的应用工况:一是车载工况功率等级高、循环波动极其复杂,功率模块温度快速变化,经常处于“极热”或“极冷”状态,消费级半导体温度可承受区间一般为-20℃—70℃,而车规级半导体一般要求温度可承受区间达到-40℃—125℃。
此外,在对抗湿度、粉尘、盐碱自然环境、有害气体侵蚀等方面,车规级半导体也有更高要求;二是汽车行驶过程中会存在振动与颠簸,功率模块长期处于高震动的工作环境,要求功率模块各组成部分具有足够的机械强度,能够在强震动环境下正常运行;三是必须确保超长使用寿命和零容错率,整车设计寿命通常在 15 年及以上,远高于消费电子产品的寿命需求,在失效率方面,整车厂对车规级半导体的要求通常是零失效;四是装配体积、重量和制造成本有严格限制。
新能源汽车电机控制器复杂严苛的使用工况对功率模块散热基板的性能和可靠性提出了很大的挑战,散热基板需在热传导性能、热膨胀系数、硬度、耐用性、体积、成本等诸多方面满足车规级使用场景的需求。
发行人所产铜针式散热基板,即用于配套电机控制器用功率模块。散热基板作为电控功率模块的重要组成部件与核心散热功能结构,通过改善功率模块散热性能,进而提升电机控制器功率密度,最终达到优化电驱动系统性能的效果。
2)散热方式与结构
从实践看,目前常见的功率模块热管理方式主要有空冷散热和液冷散热。空冷散热一般分为自然对流散热和强迫对流散热,自然对流的散热路径主要是芯片将热量传递给散热器上的翅片,热量通过翅片自然对流散发,其优点是结构简单可靠,但由于自然对流冷却的热交换系数较低,因此无法满足大功率模块的散热需求。强迫对流是在自然对流的结构基础上增加散热风扇,通过加速翅片表面的空气流动性提高散热效率。虽然强迫对流散热在一定条件下可以满足部分大功率模块的散热要求,但因风扇的存在,需要增加额外的通风结构设计,其体积一般较大,且同时会有噪声,因此空冷散热并没有在车规级功率模块中得到广泛使用。
目前,车规级功率模块采取的主流散热方式为液冷散热,其体积较小且性能稳定可靠。而液冷散热又分为间接液冷与直接液冷,两者结构区别如下:
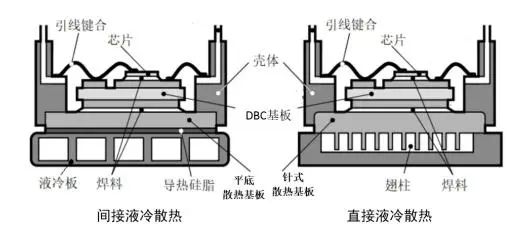
相比间接液冷散热,直接液冷散热不需要导热硅脂,也无需使用液冷板,模块整体热阻值可降低 30%左右,因而已成为车规级功率模块的主流散热方式,包括英飞凌、博世、安森美、日立、中车时代、斯达半导等在内的知名厂商生产的车规级功率模块均主要采用直接液冷散热,搭配针式散热基板。针式散热基板与平底散热基板对比如下所示:
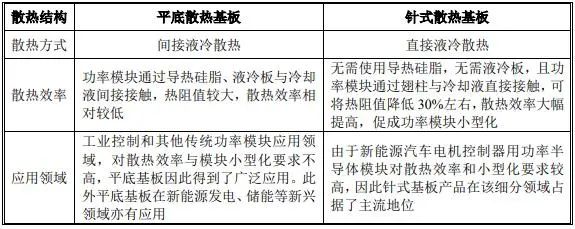
(2)产品发展历程
英飞凌作为全球车规级功率半导体领域的龙头企业,其对配套的散热基板要求较高,产品除需在热导率、热膨胀系数、硬度等性能指标方面表现优异,还需要兼具性价比和经济性。英飞凌采用的针式散热基板产品演化历程,较为全面地反映了该产品的技术发展路径。
以英飞凌代表性的 HybridPACK™系列功率模块为例,从基板材料和生产工艺角度,其配套的针式散热基板已经经历了四次演变,具体过程如下:
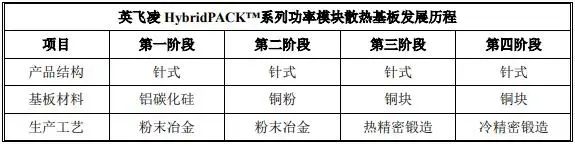
如上表,从基板材料看,散热基板经历了从铝碳化硅到铜粉、铜块的演进;从生产工艺看,散热基板经历了从粉末冶金到热精密锻造,再到冷精密锻造的演进。随着产品阶段的演进,散热基板性能逐渐优化,产品性价比逐步提高。
1)基板材料
散热基板作为整个功率模块的力学支撑与重要的散热通道,对其综合性能有较高要求,需要具备高热导率、与芯片及覆铜陶瓷基板相近的热膨胀系数和一定的硬度,同时还要兼具性价比。目前车规级功率模块散热基板材料主要包括铜、铝碳化硅和铝等,各材料主要情况如下:
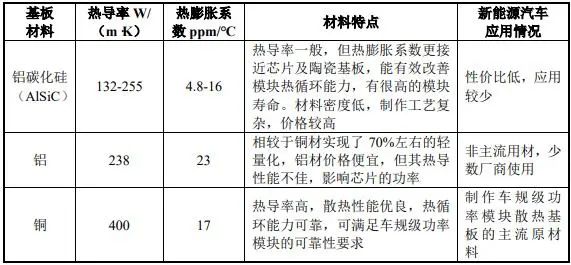
热导率与热膨胀系数是散热基板最重要的两项性能指标。热导率越高,材料导热性能越好。此外,由于功率模块由不同材料封装而成,芯片、覆铜陶瓷基板、散热基板等具有不同的热膨胀系数,高温条件下具有不同热膨胀系数的材料会在结合界面产生热应力,当热应力超过材料的极限阈值,将会导致材料结合界面断裂或损伤,因此散热基板需要具有与芯片、覆铜陶瓷基板相接近的热膨胀系数,以提高模块热循环可靠性。
在早期,由于铝碳化硅热膨胀系数相比铜更接近芯片和覆铜陶瓷基板,可有效避免结合界面的热应力,减少材料断裂和损伤,提高功率模块可靠性,因此在散热基板发展早期阶段得到了运用,但铝碳化硅制作工艺复杂、成本较高,热导率较低。英飞凌等功率模块厂商通过改进封装设计和工艺,提高焊接结合界面的可靠性,有效解决了铜材基板材料的热循环可靠性问题。采用铜材散热基板封装的功率模块,可经历上千次热循环后焊接面仍无明显退化,达到了车规级功率模块的要求,加之铜材热导率高于铝碳化硅,工艺成本较低,因此铜材已取代铝碳化硅成为制作散热基板的主流材料。
除铜和铝碳化硅外,亦有少数厂商使用铝材制作散热基板。铝材相较于铜材价格更为低廉,但其热导性能不佳,且热膨胀系数与芯片、覆铜陶瓷基板匹配性较差,采用此方案的车规级半导体厂商较少。
2)生产工艺
针翅结构的铜散热基板,是一种成形难度高且精度高的精密结构件,对生产工艺要求严格,目前主要包括粉末冶金技术和精密锻造技术,其中精密锻造又可分为热精锻与冷精锻。
A.粉末冶金技术
金属粉末注射成型技术(以下简称“MIM”)是将现代塑料注射成型技术引入粉末冶金领域而形成的一门新型粉末冶金近净成形技术,其基本工艺过程是:选取符合 MIM 要求的金属粉末和粘结剂,在一定温度下采用适当的方法将粉末和粘结剂混合成均匀的喂料,经制粒后注射成型,获得的成型坯经过脱脂处理后烧结致密化成为最终成品。
MIM 工艺在小型化、高精度、高难度形状的精密零件制造领域相比较于传统加工方法具有明显优势,具备较强的竞争力。但 MIM 工艺也存其自身的局限性:①由于使用了大量的粘结剂,烧结过程收缩率较高,一般可达 13%-25%,内部易产生孔隙,存在变形控制和尺寸精度控制的问题,且每批次产品烧结收缩率会受各种环境及原料等因素影响,影响产品合格率;②对原料粉末要求很细,粉末原料的价格一般较高,限制了该技术的广泛应用;③制程工序较多,流程较为繁琐。
B.精密锻造技术
精密锻造成形技术是指零件成形后,仅需要少量加工或不再加工,就可以用作机械构件的成形技术,即制造接近零件形状和尺寸要求的毛坯,目前该技术广泛运用于大批量生产结构相对复杂的零部件。
热精锻成形是指在再结晶温度以上进行锻造的精锻工艺。因为变形温度高,在进行锻造时材料的变形抗力低,塑性好,所以易于成形几何形状复杂的零件。热精密锻造的优缺点较为明显,其优势在于高温可减少金属的变形抗力,因而减少坏料变形所需的锻压力,对处理较硬的金属时较为高效,对模具设计要求不高。同时热锻使锻压设备吨位大为减少,可节约设备购置成本。热精锻劣势在于锻件冷却过程存在热胀冷缩现象,影响锻件精度;高温下锻件表面易产生氧化或烧损缺陷,影响产品表面质量;锻造过程能耗高,增加能耗成本。
冷精锻成形是指在常温条件下的锻造加工,利用安装在设备上的模具,在强大压力和一定速度下使金属材料从模腔中挤出,从而获得所需形状、尺寸以及具有一定力学性能的锻造方法。冷精锻技术的成形精度比热精锻要高,在精密成形领域有着独到的优势,具体优点包括:①工件精度高,产品尺寸一致性好,形状和尺寸容易控制;相比热精锻可避免高温导致的外形误差,产品表面无氧化和烧损等热加工缺陷;②零件强度性能好,冷锻产生的加工硬化效果可使产品的硬度显著增强;③能源消耗小。但冷精锻技术对模具的要求以及工艺技术的要求较高。

结构相匹配才能锻造出合格的产品,好的模具可以在提高产品良率的同时维持模具的耐用性。针翅结构的铜散热基板具有成形难度高且精度高等特点,终端运用于新能源汽车,下游客户对产品精度、硬度、表面粗糙度等指标要求较高。散热基板上分布的铜针极为密集,成百上千的铜针对模具强度的设计合理性提出了很大的挑战。纯铜作为一种锻压材料需要比铝高出 2-3 倍的变形压力,使得模具和锻压设备承受非常高的应力。如果模具设计不合理或达不到要求,就会产生应力集中和应力疲劳的问题,从而使得模具寿命得不到保证,并造成成形缺料、脱模变形等一系列问题,进而无法实现大批量生产。
(4)行业发展前景
新能源乘用车持续高速增长、商用车新能源化进程加快、交通工具电动化浪 潮全面开启等多重因素给车规级功率模块散热基板行业长期发展带来重要机遇, 行业发展空间巨大。
1)新能源乘用车持续高速增长
随着生活水平的不断提高,消费者越来越重视汽车的驾驶体验和舒适性,相 较于燃油汽车,新能源乘用车在驾驶体验、用车成本、智能化等方面具备先天优 势。驾驶体验方面,新能源乘用车因瞬间输出扭矩大,动力响应更加快速平顺, 同时还有更低的噪音和震动,驾乘体验更加平稳舒适;用车成本方面,充电费用 远低于燃油成本,且新能源乘用车保养成本较低;智能化方面,燃油车受制于传 统的电子电气架构系统,加之电池较小储能能力不足,难以实现整车智能化。随 着动力电池能量密度和性能的整体提升,新能源乘用车的续航能力得到显著增强, 充电桩覆盖率的稳步提升也使得出行更加便捷,因而能够满足大部分出行需求。
综上,由于新能源乘用车在驾驶体验、用车成本、智能化等方面的优势,其 市占率已大幅提升。而随着全球主流汽车强国对新能源汽车的政策支持、供应链 及充电桩等配套设施的日益完善、消费者对新能源汽车接受度不断提高,新能源乘用车销量仍将在中长期内保持高速增长趋势,市场占有率也将持续上升。
根据国际能源署数据,2021 年全球新能源乘用车市场占有率为 8.6%,2025年、2030 年有望分别达到 20%和 36%;销量方面,2021 年全球新能源乘用车销量约 660 万辆,2025 年、2030 年分别有望达到 1,870 万辆和 4,100 万辆,年复合增长率约 22.50%。
2)商用车新能源化进程加快
商用车新能源化,对推进绿色交通、降低碳排放有重要意义。目前,新能源商用车的发展与乘用车相比还存在一定差距。但受技术进步、补贴政策推动、配套设施的建立、用电成本下降等因素影响,商用车正在成为新能源汽车市场的重要组成部分,各级政府部门出台了一系列政策措施支持新能源商用车的发展。
以用途和负载量划分,新能源商用车可分为轻卡、重卡、大巴等类型。其中,以城市内部物流为主要运用场景的轻卡(轻型货车/物流车),是未来新能源商用车的主要增长点。
公路物流可分为城市物流和城际物流。城市物流以城市内部日常生活用品运输、快递和小件货运为代表,由于成本限制,纯电动物流车普遍续航里程不超过300km,加之整车自重大且动力系统多为永磁同步电机,天然利于轻载场景,因此城市物流将成为新能源轻卡的重要应用场景。随着网上购物兴起,快递物流业发展迅速,加之精准送达等需求影响,衍生了生鲜、代购等新的同城模式,同城货运规模增长迅速,带动了新能源物流车需求增长。目前,电商物流、快递配送、城市配送领域已经开始逐步用新能源轻卡替代传统燃油车辆,发展潜力巨大。
城际物流以重卡为主,对车辆的安全性、承载力、续航里程、维修便利性要求较高。随着国内外新能源重型卡车的推出,城际物流的电动化进程也即将开始。
2022 年 12 月,特斯拉向首批用户交付了 Tesla Semi 电动半挂卡车,该车搭配三电机系统,满载质量 37 吨,续航里程可达 800 公里,该车型的发布与交付,标志着物流电动化迈入新的阶段,物流电动化的替代空间进一步扩大。
新能源大巴领域,由于政府政策的推动,我国主要地区均出台了新能源公交车采购更新计划。深圳、广州、北京、上海等一线城市公交车辆已基本实现电动化,三四线城市客车电动化也在加速推进。随着动力电池成本下降和续航里程增加,未来新能源大巴将由短途客运和景区内摆渡逐渐进入公路客车领域,将进一步成为城市客车主流。新能源大巴符合绿色低碳循环发展的时代背景,从目前大巴市场电动化率来看,未来新能源大巴仍有较大的市场空间。
根据国际能源署预测数据,2021年全球新能源商用车销量为29.19万辆,2025年、2030 年分别有望达到 203 万辆和 457 万辆,年复合增长率约 35.75%。
3)交通工具电动化浪潮全面开启
交通领域的电动化是近年来最深刻的技术变革之一,除新能源汽车和依靠电力牵引的高铁、地铁外,电动化正逐步向电动轮船、电动飞机等领域扩展。
船舶是河运和海运的主要载体,整治船舶污染,推动船舶动力的电动化,是航运业绿色发展的趋势,也是双碳背景下中国内河航运的必然需求。新能源汽车领域的技术发展,对促进船舶电动化起到了非常关键的作用。近年来,我国陆续出台了《内河绿色船舶规范》《纯电池动力船舶检验指南》等技术标准,推动电动船舶行业发展。过去几年,中国纯电动船舶实现了快速发展,目前国内中短途运输、中小量运输的内河航运船舶上已启动电动化,各地推出的短途轮渡及景区游览船舶等电动化趋势明显。
出于减少碳排放和降低燃油成本的需求,以电动化推进技术为结合点,世界各大航空企业与汽车企业已经开始相互渗透、跨界融合发展。据统计,全世界范围内已涌现出上百家电动飞行企业。目前,市场上的电动飞行产品速度基本处在120km/h-250km/h 之间,续航里程多在百公里左右,理论上已能够满足短途的航空需要。随着电池技术与电机技术的进一步发展,在短距离商业化载人领域,电动飞机有望实现对传统燃油飞机的取代。
【免责声明】文章为作者独立观点,不代表功率半导体生态圈。如因作品内容、版权等存在问题,请于本文刊发30日内联系功率半导体生态圈进行删除或洽谈版权使用事宜。
暂无评论哦,快来评论一下吧!
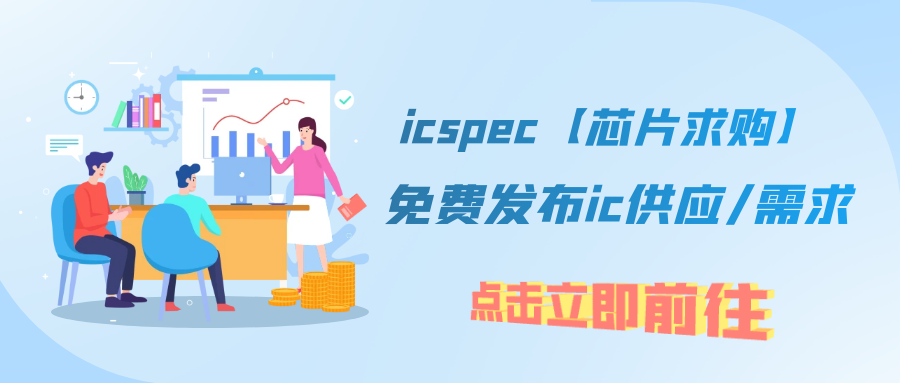
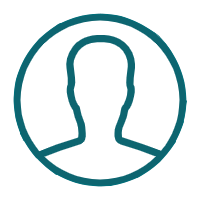