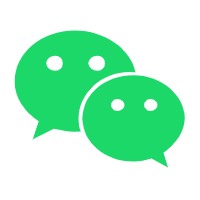
产品或系统的实际可靠性性能是设计、组装和使用的函数。
设计期间做出的决策主要创建内在的可靠性能力性能。
所选组件、制造、运输和安装都会增加产品的可变性和误差,通常会降低实际的可靠性性能。
使用条件和维护增加了另一层可变性,再次降低了可靠性能力。
了解客户的环境并在开发计划的早期使用剖面文件允许团队创建设计并控制制造过程,从而最大限度地减少各种可变性来源的影响。
可靠性工程的一个方面是在设计和制造过程的开发过程中与团队合作,以了解许多决策对最终可靠性性能的影响。
整个开发生命周期的可靠性考虑
可靠性可能或可能有现有的程序或指南来支持开发团队。
您的组织可能已经拥有一系列工具和流程,它们可以补充实现足够的可靠性性能。例如,能够在现有产品开发周期内工作,可以在生命周期的适当时间进行可靠性考虑和评估。
·在产品开发的概念阶段,我们应该专注于设定可靠性目标。
·在详细设计阶段,可靠性通过应力强度或降额分析在组件选择中发挥作用。
·在组件鉴定过程中,表征潜在组件参数的可变性可能会提供对潜在系统失效根本原因和控制计划建立的见解。
·在制造过程的开发过程中,考虑互连、装配、连接、成型、制造或基本上过程中任何步骤的可变性,使可靠性工程师能够了解错误、不符合规格的组件或子系统的相对机会,并最终过程能力对可靠性性能的影响。
与现有开发支持工具和流程集成
生命周期开发过程包括阶段关口评审。
每个阶段概述了一组要完成的任务,然后在程序进入开发过程的下一阶段之前对其进行评审。可靠性是否具体列在任务集中是产品的重要性能特征。因此,合并可靠性元素认为现有的生命周期/阶段关口流程使可靠性对整个开发团队可见。
开发工程师希望创建一个有效的设计或过程,并且随着时间的推移有效(可靠)。
鉴于产品功能性能的不确定性,开发工程师通常会在最终确定设计或流程之前使用一系列不同的工具和技术来评估选项。
一些例子:
·当开发工程师进行有限元分析以评估产品机械元件的性能时,过应力、应力集中、循环载荷、冲击或冲击载荷、热循环、材料特性随时间的变化(氧化、例如),更多允许现有的FEA研究也考虑潜在的可靠性风险和性能。
·当原型可用时,初始评估通常包括功能性能,然后是一组评估以确定在一系列预期应力条件下的性能。对每个失效进行剖析和评估,以进行可能的设计或过程改进。风险评估、环境测试、应力测试和失效分析的可靠性工程工具已经在一定程度上使用。将可靠性工程专业技能和知识添加到流程中可增强开发团队最大限度地从每一轮原型中获得的信息的能力。详细的根本原因分析使团队能够有效地理解和解决失效。
·由于供应链提供样品和首批样品供考虑,开发团队已经评估了这些组件的功能性能。添加老化的可靠性考虑或可变性对性能的影响,使团队能够识别并可能减轻可靠性问题。由供应商设计和制造的一组电源线可变性测试可能会揭示子系统设计或制造中的弱点。
·随着制造过程的发展,工程师可能会进行试运行以评估吞吐量和最终产品质量。例如,结合潜在缺陷的可靠性考虑,允许过程评估扩展到初始产品性能之外。对正在进行维修过程的装置进行加速寿命测试可提供有关该过程潜在退化的信息。
·开发团队将采用的许多现有步骤可能已经包含可靠性工程的元素。例如,增强这些元素,扩展一些元素,并结合可变性或老化的影响,使整个团队能够做出明智的决策,包括他们的决策对可靠性性能的影响。
概括
基本思想是可靠性是开发过程中做出的许多决定的结果。
增强现有开发工具的信息、洞察力和能力以考虑对可靠性绩效的影响,是在整个组织中有效整合可靠性思维的一种方式。
暂无评论哦,快来评论一下吧!
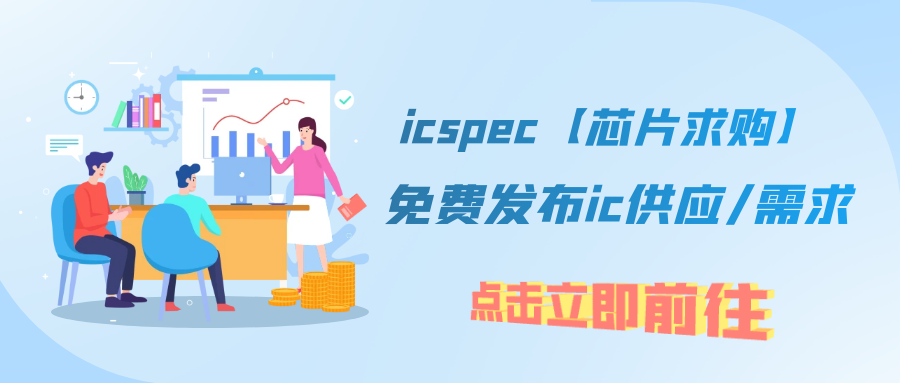