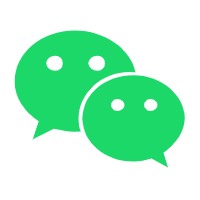
在汽车生产制造中,有很大一部分金属零件采用冲压加工成型的方法得到,冲压工艺是汽车生产的一种重要工艺方法。冲压加工具有生产效率高、成本低、精度一致性好和材料利用率高等特点。
车身上的各类覆盖件,车内支撑件等大量的汽车零部件都采用冲压工艺加工制造,冲压件在汽车零部件中占有很大比例,所以冲压加工方式的水平和能力,在很大程度上决定着我国汽车制造的成本和质量,也影响着其他包含冲压加工生产的行业的技术进步。
汽车冲压件在冲压成型过程中,由于模具配合和振动等原因,经常出现表面起皱、面畸变、局部凹陷及凸起等现象,导致汽车冲压件表面产生较大的形状误差,甚至成为废品,典型的几类冲压件表面缺陷如图所示:
各类冲压缺陷的存在会对冲压件的使用造成不同程度的影响,如汽车车身外覆盖件的表面质量直接影响喷漆后局部目视效果,影响产品的外观和后续销售。
01
汽车冲压件检测现状
目前在汽车冲压件生产中,对冲压件表面质量的检测主要有目视检测、触摸检测、油石打磨、涂油检测和检具检测等方法。
其中,目视检测主要用于可视结构的检测,如料边和棱线;触摸检测主要用于表面凸起和凹陷的检测;油石打磨用于检测外表面缺陷;检具检测用于孔径和特殊孔的检测, 几种传统的冲压件表面质量检测方法如图所示。
传统的冲压件表面缺陷检测方法具有如下不足:
1) 检测效率低, 结果不可靠
传统的汽车冲压件缺陷主要依靠检验人员目视检测,需要专门的检测人员进行检测,时间和精力投入都很大,检测的结果容易受到检测人员的主观性影响,不同的检测人员得到的检测结果差异较大,可靠性较差,可信度低;
2) 质量跟踪比较困难
传统检测方法的结果粗糙,缺少标准的、量化的指标来评价汽车冲压件的质量。同时,检测数据的缺失使得后期建立完整的质量跟踪体系存在着很大的难点,不利于冲压工艺方法的进步;
3) 产品数字化集成困难
由于传统的冲压件检测方法存在的缺点,检测过程和结果过于依靠检测人员的工作经验,检测数据也不能及时录入检测部门的数据库这就为企业不同部门之间的技术交流增加了困难,甚至引起生产部门,技术部门和质量部门之间的推诿纠缠,不利于企业的技术进步。
机器视觉检测技术作为近些年来被广泛使用的非接触式检测方法,在检测效率和检测精度方面有着其他检测方法无法比拟的优点,可以克服人工检测容易视觉疲劳的缺点,特别适合大批量大规模生产的冲压工艺产品表面缺陷检测。
02
冲压件表面缺陷分析
冲压件作为汽车制造行业中应用十分广泛的零部件,其表面缺陷产生的机理与种类与其他金属加工方式有所不同。
通常所说的冷冲压工艺是在常温条件下由安装在冲压机上的冲压模具对金属毛坯进行相关冲压工序操作(如冲裁, 拉延, 成形, 落料和冲孔等) 获得零部件的一种压力加工方式,在不同的冲压工序中,容易产生的各类冲压缺陷也不尽相同。
汽车冲压件常见的表面缺陷种类以及具体呈现形式如图所示:
1) 压痕:压痕缺陷产生的工序不确定,多是由于冲压异物挤压表面导致的。大多数情况为拉延工序时有物料导出不畅通,以至于残留的废料掉入模具内使得下面工序挤压导致了压痕缺陷。
2) 划痕:此类缺陷产生的原因主要包括以下几个方面,比如工件原材料本身的自带缺陷,零件运输过程中接触干涉导致的缺陷,成品装箱接触刮碰产生,加工工位需要转运摩擦碰撞产生;
3) 少孔:此类缺陷产生的原因包括冲头漏装或折断,冲压件少孔是产品设计和要求所不允许的;
4) 边缘缺料:冲压件边缘缺料缺陷发生在拉延工序,主要原因是由于模具与冲压件定位有误差,冲压位置不准确,或者是材料流动速度偏快导致了缺料缺陷
03
光源系统分析
选择和设计光源系统的规律和原则主要包括包括以下几个方面:
1)增强待处理的物体特征;
2)减弱非检测目标的物体和降低相关噪声;
3)不引入额外的干扰特征。
冲压件表面压痕和划痕缺陷的打光方式较为复杂,主要原因有两方面:一方面是待测工件表面结构复杂,表面光亮,反光情况严重;另一方面是缺陷细微,难以通过照明突出。
针对可能包含少孔缺陷和边缘缺料缺陷的工件的打光对比试验, 采取了以下打光方式:
环形光源照明方式
环形红光照明效果
04
检测要求及相机选择
选择合适的工业相机首先应当考虑的是相机的分辨率,相机像素精度的选择方法可以依据一个方向视野的大小除以单方向分辨率得到,即相机单方向分辨率 =单方向视野范围大小 ÷ 理论精度。
本文所研究的汽车冲压外观件和结构件尺寸以及其缺陷大小尺寸见表:
结合检测缺陷任务,功能件需要整体拍摄并在视野范围内识别缺陷,而针对外观件来说,其尺寸较大, 缺陷较小,不能整体拍摄(工件占全视野),并根据在大视野范围内识别小缺陷。
本文先按照功能件缺陷大小选择相机分辨率, 再用外观件验证。
按照目标物体占到视野百分之七十计算,单方向分辨率:
200 ÷ 5 ÷ 0.7 = 57.14
假设选择 130 万像素(1280 × 1024) 相机,拍摄外观件时视野范围内外观件大小为 X ,则有:
X ÷ 0.2 ≤ 1024 ÷ 3
X 为68.27,意味着视野范围内包含的外观件单方向尺寸不超过68.27mm,即可有效稳定识别划痕和压痕。
图像采集硬件平台
05
外观缺陷检测
表面压痕检测
包含压痕和划痕缺陷工件表面结构复杂,曲面特征较多,不同的打光效果会对拍摄效果造成很大影响。
最终识别出的压痕缺陷等效椭圆短半轴长为 4.94128,长半轴为 30.9174,面积为453(图中红色缺陷,对应实际工件缺陷宽度为 1 毫米。
冲压件压痕初始图像
冲压件压痕缺陷图像
表面划痕检测
冲压件表面划痕的特点是比压痕更加细微,肉眼检测需要从侧面调整角度观看才行,而且肉眼检测大量工件会造成视觉疲劳,从而导致漏检、误检。
采取红色无影光源侧向打光,突出待检测部位划痕, 使得划痕缺陷成为高亮度特征。
冲压件划痕缺陷初始图像
冲压件划痕缺陷识别图像
检测出的划痕缺陷区域等效椭圆短半轴长为 4.3264, 长半轴为 93.1809, 面积为1009。按照宽度为 0.2 毫米, 在此检测环境下, 可以检测的划痕最小宽度为 0.1 毫米。
申明:感谢原创作者的辛勤付出。本号转载的文章均会在文中注明,若遇到版权问题请联系我们处理。
----与智者为伍为创新赋能----

联系邮箱:uestcwxd@126.com
QQ:493826566
暂无评论哦,快来评论一下吧!
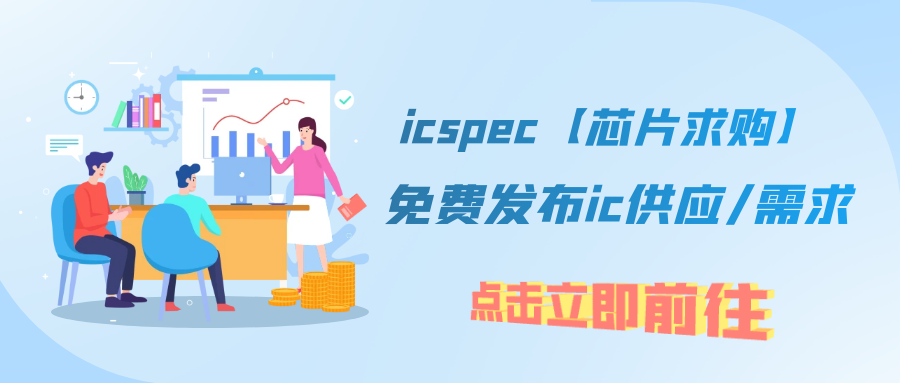
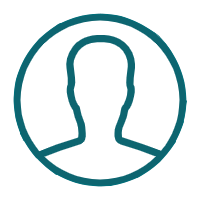