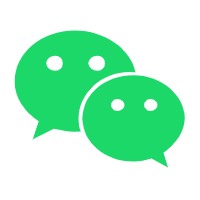
微流控技术最初源自于微机电系统(micro-electromechanical system, MEMS)在微量流体操控方面的研究,形成于20世纪90年代初。最近十年来,伴随着分析化学和生命科学的蓬勃发展,由于微流芯片系统具有试剂和能量消耗少、检测和分析灵敏度高、检测时间短、可将多种功能集成化程度高等优势,在纳米纤维合成、纳米复合物制备、量子点合成、微纳米颗粒制备、电化学传感器、生物化学传感器、细胞生物学、分子生物学等领域得到了广泛的应用。通过微流控技术,可以将复杂的化学或生物分析合成过程整合在一块芯片中完成,实现了微全分析系统(μTAS)或被称为芯片实验室(lab-on-a-chip)。
初期的微流控芯片加工技术完全继承自MEMS加工技术,步骤都需要在超净间内使用精密微加工设备完成,芯片的设计加工成本非常高昂,严重阻碍了其在分析化学和生命科学领域的推广应用。时至今日,欧美一些微流控技术公司生产的标准化玻璃或聚合物材料微流控芯 片单片售价仍在数十到几百美元,对于微流控芯片在生物、化学、医学等领域的应用和产业化也形成了阻碍。
近年来,机械、电子、化学、生物等领域的研究者根据其在各自领域的专长和经验,探索使用了多种低成本微加工方法。从相关论文的发表情况看,在Web of Science核心数据库中,从2000年到2018年1月以“低成本(low-cost)”和“微流控芯片(microfluidics)”为关键词的论文发表数量,呈逐年稳步增长的趋势,目前,该方向每年的SCI论文发表数量为550 篇左右。
低成本微流控芯片的加工材料
硅和玻璃是最早用于微流控芯片的基体材料,主要是由于其加工方法可以直接套用MEMS和微电子领域的加工方法。硅和玻璃材料价格昂贵且不易加工,在微流控芯片的发展过程中很快就被以各类聚合物为代表的低成本材料所替代。现有各类微流控芯片的加工方法中,可供选择的低成本材料很多,有各类弹性体材料、热塑性聚合物材料、热固性聚合物材料、纸材料、生物材料等。本文的讨论中,将常见的可用于低成本微流控芯片加工的材料分为聚合物材料、纸材料、其他材料三类分别进行介绍。
聚合物材料
弹性体材料
本文所述的弹性体材料指的是能够在弱应力下发生显著形变,应力松弛后能迅速恢复到接近原有状态和尺寸的聚合物材料。聚二甲基硅氧烷(polydimethylsiloxane, PDMS)是目前在微流控芯片领域应用最为广泛的弹性体材料,PDMS用于微流控芯片最早在1998年由Whitesides等提出,PDMS具有价格低廉、光学透明、生物兼容性好、具有一定透气性等优点,是低成本微流控芯片的理想材料(如图1所示)。PDMS在微流控芯片加工中往往通过模塑成型的方法在表面形成微结构,其翻模精度甚至可以达到纳米(nm)级别。然而,PDMS也有通道易变形坍塌,对通道内流体有少量吸收等缺点。PDMS的加工和键合方法将在本文的低成本加工部分进行较为详细的介绍。
图1 基于PDMS材质的液滴发生微流控芯片
热塑性塑料
热塑性塑料是日常生活中最为常见且应用广泛的材料,价格非常低廉,热塑性塑料可以在一定温度条件下变软后进行塑形。可用于低成本微流控芯片的热塑性材料种类很多,主要有聚甲基丙烯酸甲酯(PMMA)、聚苯乙烯(PS)、环烯烃类共聚物(COC)、聚碳酸酯(PC)、聚对苯二甲酸(PET)、聚氯乙烯(PVC)等。
热塑性塑料中,PMMA由于材料成本低、热加工和光学性能良好,基于PMMA的微流控芯片在各类生命科学和医学研究中具有广泛应用;PS具有优异的生物兼容性,作为微流控芯片的基体材料在细胞培养等领域具有显著优势;COC作为一种较新的非晶性共聚高分子材料,与PMMA等热塑性材料相比,在紫外光波段具有优异的透过性能和更好的热稳定性,同时吸水性只有PMMA的1/10,COC芯片在大多数情况下(非极端温度情况)可以直接替代昂贵的玻璃芯片。
纸材料
纸基微流控芯片是通过各种方法将疏水材料渗透入亲水的纸纤维中,通过疏水材料的“围墙”控制亲水纸纤维内的流体流动,从而形成了纸基微流控芯片,常见的喷墨打印机、丝网印刷、3D打印机、蜡打印机甚至蜡笔都可以被用来加工低成本的纸基微流控芯片。在纸张选择上,常见的有Whatman系列滤纸或色谱分析纸。与聚合物材料微流控芯片需要封闭流道不同,纸基微流控芯片由于液体在纸张纤维内部运动,往往不需要对流道进行封闭,即开放式流道(open-channel)。
图2所示的用于血细胞分离和血清蛋白检测的纸基微流控芯片,利用了浸蜡的方法定义了液体在纸纤维内流动的通道,随后通过纸纤维的孔隙对血浆和血细胞进行分离,最后通过显色测定血清蛋白含量。纸基微流控芯片由于材料和加工成本低廉,已经被广泛应用于各类医学和生命科学检测研究和应用中,如唾液乙醛检测、重金属检测、血糖检测、乳酸检测等。
图2 用于血细胞分离和血清蛋白检测的纸基微流控芯片
低成本微流控芯片的加工与键合方法
低成本微流控芯片加工方法
选取了常用的低成本微流控芯片加工方法进行介绍。
微模塑成型
由于PDMS材料在微流控芯片加工领域的广泛应用,基于PDMS的微模塑成型成为目前最为常见的微流控芯片加工方法。其中,使用SU-8光刻胶作为模具对PDMS进行模塑成型较为常见,将SU-8光刻胶旋涂在硅片上并进行光刻,根据不同型号SU-8光刻胶和旋涂速度的控制,其厚度可以在十几到一两百微米范围内自由调节;将PDMS主剂与硬化剂10:1混合去除气泡后缓慢倾倒在SU-8微结构上,加热硬化;将PDMS从SU-8模具上小心揭取,模具可以重复使用;将PDMS与玻璃等基底材料进行氧等离子处理后键合。
激光烧蚀
这里的激光烧蚀特指使用波长为10.6 μm的二氧化碳激光在聚合物材料表面进行烧蚀加工微流道的方法。使用激光烧蚀方法加工微流道,其优点在于:加工过程简单快捷,一次烧蚀即可完成加工;材料适用范围宽,大部分聚合物材料和玻璃等均可使用该方法在表面加工微流道。缺点在于:在聚合物材料材料表面加工的微流道内壁凹凸不平,存在大量气泡,可能需要通过化学方法进行处理;在聚合物材料表面加工流道两侧有熔融材料抛出再凝固形成的凸起,不利于后续键合;加工精度有限,仅适用于流道宽深度大于80 μm的应用。激光烧蚀方法在低成本微流控芯片领域的应用,目前还集中在单一聚合物材料应用上,从未来的发展方向看,其在基于可降解生物塑料、纸、导电塑料等材料的微流控芯片加工领域还有较大的发展空间。
2D/3D打印
2D打印指办公和实验场合常见的激光打印机、喷墨打印机、蜡打印机、丝网印刷等加工微流控芯片或微流控芯片倒膜模具的方法,3D打印是利用近来发展迅速的3D打印机直接打印微流控芯片或倒模模具的技术。2D打印微流控芯片通常应用在纸基微流控芯片中,通过疏水性墨水的浸透作用在亲水纸材料中包围形成微流道,图案精度由打印机精度或丝网网孔决定,通常在80~400 μm之间。此外,还可以利用喷墨打印或丝网印刷在玻璃或聚合物基底上直接沉积PDMS、SU-8等材质的微结构,形成微流控芯片;如果使用含有银纳米颗粒的导电墨水,还可在微流控芯片表面打印电极。图3(a)、图3(b)为丝网印刷的基本原理,通过丝网印刷方法加工的基于紫外感光介质浆料(5018A,Dupont,USA)的微流道和银电极。
图3 基于丝网印刷的微流控芯片
使用3D打印对微流控芯片进行加工,主要有微立体光刻(stereo-lithography)、熔融沉积成型(FDM)等方法,其中熔融沉积成型3D打印机由于价格相对低廉可用于低成本3D微流控芯片的加工。熔融沉积成型技术既可以直接打印PC、PLA、ABS(acrylonitrile butadience styrene)等材料制成3D微流控芯片,也可以打印用于PDMS倒模的模具。但目前商业化熔融沉积成型设备的精度在100~500 μm之间,距离大部分微流控芯片的应用需求还有一定差距,且适于微流控芯片使用的透明打印耗材选择有限,芯片加工速度与本文介绍的其他方法相比也较慢。
注塑成型
注塑成型是在塑料加工领域使用广泛的加工方法,近年来伴随微注塑技术的发展,研究者开始尝试使用注塑成型的方法加工微流控芯片,常见的用于微流控芯片的注塑材料有PMMA、COC、PDMS等。传统上,使用注塑方法加工微流控芯片需先加工模具,耗时长且模具价格昂贵。在低成本微流控芯片加工中,有别于传统金属模具,Hansen T S等人使用加工在镍表面的SU-8光刻胶作为注塑模具,模具反复使用300次后制品质量稳定,显著降低了成本和模具加工时间。其优势在于重复性好、加工速度快、可以加工3D微流控芯片,适用于大规模微流控芯片的加工;缺点是灵活性差,芯片结构变动时需要重新开模,模具成本较高。
低成本微流控芯片键合技术
除纸基微流控芯片可以采用开放式流道外,其他各类型微流控芯片在微结构加工完成后都需要在流道上方覆盖一层材料(盖片)完成流道的封闭,即微流控芯片的键合。盖片材料与基底材料可以是同类、同厚度材料,特殊用途时也可对不同类型和厚度的材料进行键合。不同于超净间内使用精密仪器设备完成的硅、玻璃芯片间的键合,近年来,研究者提出了各类低成本的微流控芯片键合方法,主要包括热压键合(thermal compression bonding)、粘合(adhesive bonding)、表面氧等离子处理键合(plasma surface treatment)以及激光焊接(laser welding)等,如图4所示。
图4 常见微流控芯片键合方法
热压键合
热压键合图4(a)是基于PMMA、PC、PS、COC/COP等热塑性材料微流控芯片较为理想的键合方法,待键合的两层材料接触并对准后,通过同时加热加压的方式完成芯片键合,加热温度略高于热塑性塑料的玻璃化温度(Tg),压力则可根据实际情况进行设定。研究者在使用热压方法对微流控芯片进行键合的领域进行了较为深入的探索,完成了PMMA/PMMA、PMMA/PS、COC/COC等材料在不同温度和压力下键合强度的研究。热塑性材料使用热压键合最常出现的失败情况是由于温度或者压力过高导致键合过程中微结构发生坍塌,实际使用中一方面需要严格控制温度和压力的设定,另一方面也可使用氧等离子或紫外光对材料表面进行预处理,降低聚合物材料待键合表面的分子量以降低表面的玻璃化温度。
粘性键合
粘性键合图4(b),是指在芯片基底材料上添加一层粘性材料,再覆盖盖片进行键合。这里的粘性材料通常是具有紫外固化性质的材料(如SU-8、干膜等),需要经过紫外曝光实现基底和盖片材料的键合。此外,非紫外固化材料如蜡也可以用来进行简易的芯片键合。除使用粘性材料外,还可在待键合材料的接触面上涂覆一层有机溶剂,通过有机溶剂材料对表面的部分溶解实现键合,缺点在于粘性材料或有机溶剂键合后在微流道内有残留,与流道内液体接触后会溶解到实验溶液中,可能严重影响实验结果。
氧等离子表面处理键合
具有微结构的PDMS基片通常使用氧等离子体对表面进行处理后与PDMS、玻璃、PMMA、PC等材料进行键合图4(c)。如果使用PDMS、玻璃或硅材料的盖片,PDMS基片与盖片需要同时进行氧等离子表面处理,从低成本加工的角度看,氧等离子表面处理设备的成本较高,实际应用中如果不具备设备条件也可使用低成本的手持式等离子电晕设备代替氧等离子表面处理。使用氧等离子表面处理对基于PDMS材料的微流控芯片进行键合,其优势在于:表面清洁无污染、键合速度较快;其劣势在于芯片清洗等操作较为复杂,且设备成本较高。
从芯片键合技术发展看,目前可逆(reversible)键合和混合(hybrid)材料键合领域的研究最为活跃。研究者尝试了各种物理和化学方法实现PDMS等材料的可逆键合,以及PDMS /SU-8等物理化学性质完全不同材料间的混合键合。
结论
针对分析化学和生命科学领域,介绍现阶段低成本微流控芯片材料和加工领域的最新技术和成果。介绍的各类低成本微流控芯片及其加工方法都是可以通过化学和生物实验室的常见材料和仪器设备加工完成的,对于分析化学和生命科学领域希望使用微流控芯片的研究者具有实践意义。
暂无评论哦,快来评论一下吧!
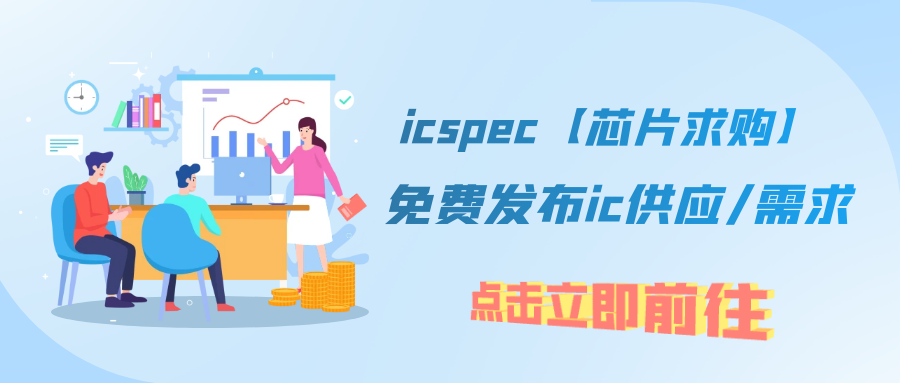
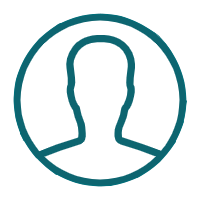