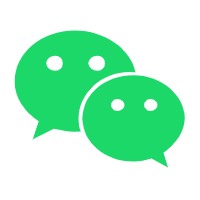
0 引言
时至今日,知道变频调速的人已经相当的普遍了。大多数人一提起变频调速,总是能和节能挂起钩来。近年来,尽管我国在能源开发方面进展迅速,但还是跟不上需求的增长,节能问题始终处于相当突出的位置。
变频调速之所以节能,主要在于把全速运行中浪费的电能节约了下来。尤其是闭环调速系统,如恒压供水系统等,实现了按需拖动,几乎完全消除了拖动系统在运行过程中的浪费。这是从大的方面实现了节能,但并不等于节能潜力已经挖掘干净了。事实上,在许多场合,还存在着大马拉小车的现象,在这一方面,还大有潜力。本文专就大马拉小车的节能技巧问题作一探讨。
1 大马拉小车的基本分析
当负载所需的功率远小于电动机的额定功率,或者负载折算到电动机轴上的转矩远小于电动机的额定转矩时,通常称之为大马拉小车。
1.1 大马拉小车时的反电动势
电动机定子侧的电动势平衡方程
1.2 大马拉小车时的磁通
1.3 大马拉小车时的励磁电流
1.4 大马拉小车存在的问题
1.4.1 功率因数变差
电动机的电流平衡方程是
图2所示,是粗略的电流矢量图。图2(a)是额定状态时的情形。
轻载时,转子的折算电流小了,而励磁电流大了。结果,合成为定子电流后,和电压的相位差角增大了,而功率因数则变小了,如图2(b)所示。
1.4.2 效率降低
磁通的增加,将增大铁心的磁滞损失和涡流损失,使损耗功率的相对值增大,效率降低。
1.5 大马拉小车的界定
有关资料表明,异步电动机的最高效率发生在负荷率为0.7~0.85 的时候,其效率曲线如图3 所示,图中的横坐标是电动机的负荷率,其计算式为
2 变频器的节能技巧
由以上分析,大马拉小车的结果,首先反映在反电动势增大。显然,如果适当减小电源电压,反电动势就可以随之减小。由式(4),磁通就可以恢复到接
近于额定值。
因此,大马拉小车节能的基本途径,便是适当降低电压。而在应用变频器的场合,节能的方法更是灵活多样。
2.1 工作频率为50 Hz时的节能方法
图4(a)所示,是大马拉小车的典型例子:当运行频率为50 Hz时,电动机的额定容量是110 kW,而负载实际所需功率只有70 kW。
针对这种情况,降低电压的方法是加大基本频率。如图4(b)所示,如把基本频率加大为60 Hz,则60 Hz对应于额定电压380 V,而在50 Hz 时得到的电压只有317 V。
2.2 低频运行时的节能方法
二次方负载在低速运行时,极易出现大马拉小车的状态。如图5 所示,曲线①是负载的机械特性,曲线②是电动机的自然机械特性,额定转矩为TMN。在全速运行时,负载转矩等于TLN,与电动机的额定转矩十分接近。曲线③是电动机在低频运行时的机械特性,有效转矩为TEA,而负载转矩为TLD,比电动机的有效转矩小得多,所以电动机处于大马拉小车的状态。
针对上述现象,节能的基本方法如下所述。
2.2.1 预置低励磁U/f比
各种变频器都设置了低励磁U/f比功能。即在低频运行时,减小U/f比,使U/f线如图5(b)中的曲线④′(曲线④为基本U/f线)所示,曲线④′通常称为低励磁U/f线。由图知,当频率为fA时,电压从UA下降为UA′。这时,电动机的磁通比额定磁通还要小,从而降低了有效转矩,使之更接近于负载转矩。
降低电压后的机械特性如图5 (a)中的曲线③′所示,电动机的有效转矩减小为TEA′,和负载转矩TLD之间的差距减小了,从而缓解了“大马拉小车”的问题。
2.2.2 自动搜索最佳工作点
变频器可以任意预置U/f比的特点,相当于在某一频率下,可以任意改变其工作电压。在任意改变其工作电压时,电流的变化规律就是电动机的电流-电压曲线,如图6 所示。
当电压偏低时,虽然磁通减小,但是励磁电流却变化不大;
另一方面,因为电动机电磁转矩的大小取决于转子电流和磁通的乘积,即
反之,当电压偏高时,一方面,由于磁通的增大,转子电流略有减小;另一方面,电动机的磁路趋向饱和,结果是励磁电流大幅度增加,在合成为定子电流
时,也使定子电流增加,如图6(a)中的A″点所示。
综合上述,得到完整的电流- 电压曲线如图6(a)所示。图中的A 点称为最佳工作点。
当负载增大时,电动机的电流和所需电压都将增大,最佳工作点向右上方移动,电流- 电压曲线也将随之移动,如图6(b)中的曲线②和曲线③所示。相应的最佳工作点如B 点和C 点所示。
某些变频器具有自动搜索最佳工作点的功能,可以在任何状态下,使运行电流为最小值,从而得到比较理想的节能效果。
3 隐形的大马拉小车现象
3.1 上限频率太低
有的用户主要利用变频器来降速,上限频率往往预置得很低。这实际上也是一种大马拉小车。
因为当上限频率低于基本频率时,电动机的有效输出功率是要减小的。
图7所示,是一个上限频率只有30 Hz 的实例。
电动机的额定容量为75 kW,但当运行在30 Hz时,其有效功率为
3.2 机械调速带恒转矩负载
机械调速大多采用齿轮箱,也有机械的无级调速器。由于驱动电动机的功率是恒定的,根据能量守恒的原理,调速器输出轴的功率也是恒定的。所以,机械调速器输出轴的机械特性具有恒功率特点,即高速时转矩小、低速时转矩大,如图8(b)中的曲线②所示。
如果用机械调速器来拖动恒转矩负载,负载的机械特性如图8(b)中的曲线①所示。[!--empirenews.page--]
十分明显的是,为了在最高转速时也能带动负载,电动机的额定转矩必须大于负载转矩。而在额定转速以下运行时,电动机将始终处于大马拉小车的状态,如图8(b)所示。
4 恒功率负载的拖动系统
4.1 卷绕机械
以某卷绕机为例:
4.1.1 负载侧的计算
就是说,在卷绕的全过程中,负载的功率是恒定的,都约等于1 kW,如图9(c)所示。
4.1.2 电动机侧的计算
电动机的额定转矩必须能够带动卷径最大时的负载转矩,故有
电动机的额定转速必须满足负载的最高转速,故有
4.1.3 解决大马拉小车的途径
可见,所需电动机的容量减小了一半。
如果最高频率达到额定频率的3 倍,则可进一步将电动机的容量减小为2.2 kW,如图10(b)所示。
电动机如果长时间在过高频率下工作,会引起轴承磨损及动平衡等方面的问题,一般不推荐在2倍频率以上运行。但卷绕机械在最高频率下运行的时间极短,随着半径的迅速增大,卷辊的转速将迅速下降。所以,上述方案是可行的。
4.2 金属切削机床
大部分金属切削机床都属于恒转矩和恒功率混合的负载,其要点如下。
4.2.1 机械特性
以普通车床为例,负载的阻转矩如图11 中虚线框内所示,等于切削力和工件半径的乘积
在切削深度和进刀速度不变的情况下,切削力F主要与切削的线速度成正比。因此,工件的转速越高,负载的阻转矩也越大。
但实际上,由于受到刀具和机床床身强度的限制,要求在大部分调速范围内,切削功率保持恒定。
因此,其机械特性具有恒功率的性质。
但在低速段,则因为切削力F要受到限制,故其机械特性具有恒转矩的特点。所以,金属切削机床的机械特性属于恒转矩和恒功率相混合的特性,如图12所示。
4.2.2 计算转速
恒转矩区和恒功率区的分界转速,称为计算转速,用nD表示。
关于计算转速nD大小的规定因机床的种类而不同,如在老系列车床中,一般规定:从最低速起,以全部转速挡数的1/3的最高速作为计算转速。例如,CA6140型普通车床主轴的转速共分24挡:n1、n2、n3、……n24,则第八挡转速(n8)为计算转速。
但随着刀具强度和切削技术的提高,计算转速已经大为提高。近年来,在一些新系列车床中,已逐渐提高为以最高转速的(1/4~1/2)作为计算转速
4.2.3 调速特点与减容方法
金属切削机床的转速调节,通常是在停机情况下进行的,在切削过程中,一般不进行转速调节。这是一个很重要的特点,应该充分利用。
根据金属切削机床停机调速的特点,传动比可以考虑分成两挡或多挡,使变频调速后的有效转矩线尽量逼近负载的机械特性曲线。以某车床为例,如图13 所示,为了便于观察,各轴上的转矩和转速都折算到负载轴上。图13 中,曲线①是车床的机械特性;曲线②是低速段变频调速后的有效转矩线;曲线③是高速段变频调速后的有效转矩线。由图可知,电动机的有效转矩线与负载的机械特性曲线十分接近。这样做的目的,是可以使拖动系统的容量尽量地接近负载实际所需的容量.
5 结语
由于历史的原因,工业设备中的电动机所驱动的负载的功率,常常远小于电动机本身的功率,这种大马拉小车的现象,浪费了设备资源,也浪费了宝贵的电力。本文分析了这种不匹配现象的本质,针对不同的负载特性,提出了不同的解决方法,值得从事设备的节能技术改造以及制定新设备的设计方案的技术人员考虑。
暂无评论哦,快来评论一下吧!
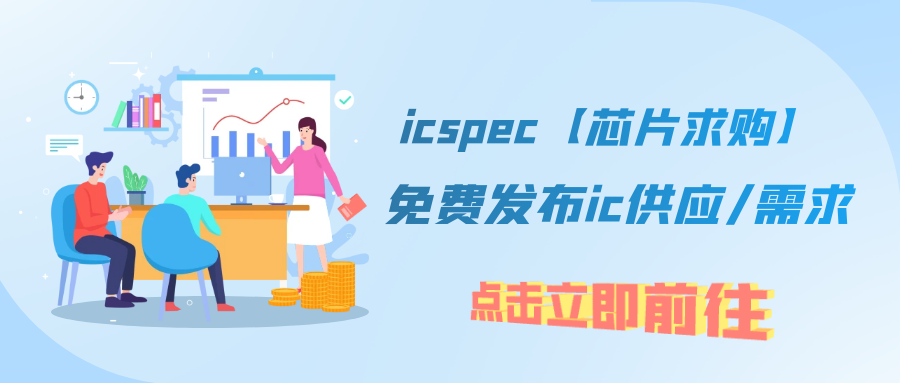