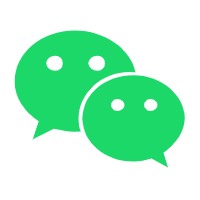
电动汽车(EV)的普及在很大程度上取决于能否成功地扩大其实际行驶范围,使其超出城市市区的行驶界限。要做到这一点,就必须稳步提高电池组的容量以及相关功率电子设备的效率。与此同时,消费者还期望缩短充电时间,并在广泛的地域范围内体验到更方便的充电方法。这两种趋势相互竞争和促进,最终推动了EV充电桩本身的发展。
电池容量和充电桩发展趋势如图1所示。在过去五年中,电池容量增加了一倍多,充电桩的供电能力几乎增加了两倍。这得益于电池化学和结构技术的飞跃,以及充电侧电路拓扑和元器件的巨大进步。
图1:电池容量和充电桩发展趋势。
EV充电桩的原型中包含大量构建模块。其中的三相交流电源,采用高效率有源器件进行整流,同时控制功率因数校正。输出电流和电压受到监控,并以400~1000V的电压馈入EV电池。而并联和隔离低压域则用于所有高压功率电子部件的控制,其中包括交直流转换器、微控制器和各种接口。
为了满足这些高性能和高效率EV充电设计的需求,罗姆公司提供了广泛的有源和无源电子器件产品组合,这些产品专门针对EV充电应用进行了量身定制,特别是碳化硅MOSFET和二极管以及配套的栅极驱动器。
碳化硅MOSFET:推动EV向前发展
碳化硅是一种宽带隙半导体,因其具有高耐压、高功率密度、低导通电阻和出色的热传导性,从而在功率电子领域占据着中心地位。这些特性都非常适合EV充电桩内的许多功能。
如图2所示,罗姆的第四代碳化硅MOSFET采用专有的沟道结构,在保持高压工作的同时,降低了有源区的导通电阻,因此该器件是目前业内损耗最低的器件,具有开关速度快、可靠性高和实施简便等特点。
图2:第四代碳化硅MOSFET的导通电阻降低效果示意图。
除了减少器件有源区的传导损耗外,寄生电容也得到了显著改善。这有助于减少这些寄生电容高速充放电时的功耗,避免自导通。最终结果是发热量大幅减少,散热片尺寸可减小40%,如图3所示。
图3:第四代SiCMOSFET开关损耗性能的改进。
第四代沟道设计的另一个重要特点是阈值电压明显提高。在典型的桥式电路中(如图4所示),经常会出现MOSFET过快导通的风险,从而导致另一个器件也因寄生Cgd耦合而意外导通。由于瞬态馈通电流的存在,这会大大增加开关过程损耗。为了减轻该影响,通常需要利用专门的负电源偏置,迫使MOSFET处于关断状态。这种额外的供电增加了成本,使设计复杂化,并引入了新的潜在故障源。
而这种第四代碳化硅MOSFET具有更高的阈值电压,可在不增加栅极负偏置的情况下实现可靠运行。即使在结温较高的情况下,这种沟道式设计也不会在快速开关过程中出现自导通。
图4:MOSFET桥式电路中的自导通效应。
由于涉及高电压和大电流,EV充电桩的可靠性至关重要。在这一应用领域中,MOSFET的一个关键可靠性指标是短路耐受时间(SCWT)。在这种第四代碳化硅MOSFET中,由于采用了独特的器件结构,尽管降低了特有的导通电阻,但仍能获得较小的饱和电流。与传统结构相比,该器件在短路条件下的耐受时间更长。如图5所示,该器件在短路条件下可保持5.54µs才失效。与之前的竞争产品相比,这是一项重大的改进。
图5:碳化硅MOSFET的短路耐受时间(SCWT)示意图。
低导通电阻、最小寄生电容和强短路耐受力的组合使这些碳化硅MOSFET极为高效可靠。在采用简单的单电源栅极偏置后,这些器件将非常适合EV充电桩内的许多高压、大功率开关应用。
碳化硅二极管:下一代汽车创新技术
高速、高压二极管是EV充电系统、尤其是LLC谐振逆变器中的关键器件。罗姆的第三代肖特基势垒二极管(SBD),采用其专有的碳化硅结构,可在实现高反向击穿电压的同时,将寄生电容降至最小。这使得反向恢复时间非常快,对工作温度也不再敏感。与传统二极管相比,其反向恢复性能也得到改进,如图6所示。
图6:二极管反向恢复时间比较。
罗姆公司的碳化硅SBD还具有出色的正向压降,从而可实现更低的功耗、极低的反向电流和对电流脉冲的高耐受性。
对于高压转换器来说,采用碳化硅MOSFET和碳化硅SBD的组合,可减少元器件总数并提高整体效率。如图7所示,前端的开关数量减少了一半,次级的二极管数量也减少了一半。
图7:使用碳化硅器件可减少元器件总数和功耗。
将栅极驱动器纳入汽车设计
在为EV充电桩设计开关转换器时,必须非常谨慎地设计驱动电路。为了帮助实现这一目标,并最大限度地降低设计复杂性,罗姆提供了一系列专为碳化硅MOSFET和其他大功率开关器件设计的全绝缘和半绝缘驱动器IC。图8所示的BM6105AFW-LB即为一款全绝缘产品。
图8:BM6105AFW-LB电路框图。
这类驱动器采用电感耦合,可将低压控制信号与高压栅极信号完全隔离开来。这对于通常采用浮动电压域设计的高压侧开关尤其有用。
而对于仅需要半绝缘的应用,可采用如图9所示的BM60212FV-C。
图9:BM60212FV-C应用电路框图。
其中,高压侧器件采用电感隔离,而低压侧器件则由控制电压基准直接驱动。这样既降低了设计复杂性和成本,又提供了安全有效的开关控制手段。
图10:集成式隔离与光耦的比较。
将电感耦合式栅极驱动器与更常见的光学隔离进行比较,可以发现显著的性能优势。如图10所示,即使在工作温度较高的情况下,电感驱动器的导通和关断时间也要快两倍以上。
(参考原文:sic-devices-for-ev-chargers)
本文为《电子工程专辑》2023年10月刊杂志文章,版权所有,禁止转载。点击申请免费杂志订阅
暂无评论哦,快来评论一下吧!
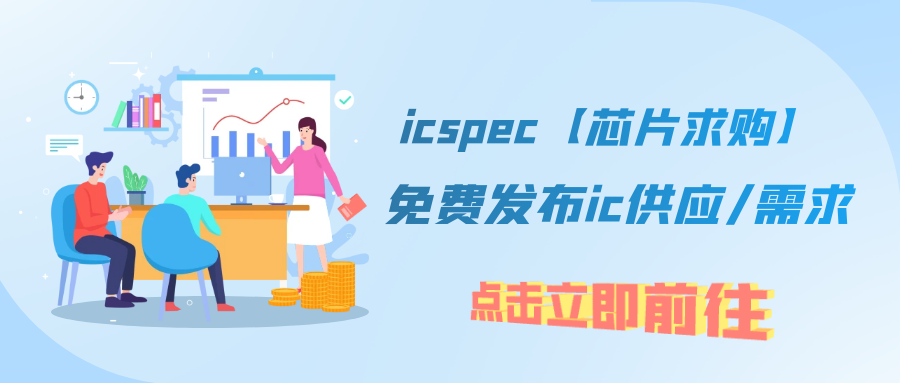