减重30%,制造成本降低40%!新趋势下这些汽车轻量化材料大有可为
来源:新材料在线 发布时间:2022-09-12
分享至微信
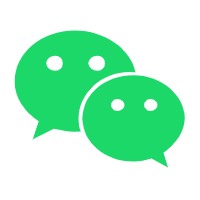
轻量化是汽车发展的大势所趋,轻量化能够降低汽车油耗、提升续航里程。各大汽车制造商纷纷加快轻量化改革,在汽车制造中寻求更为轻量的材料与工艺。
汽车轻量化远期市场空间广阔,目前可以通过三种方法来实现汽车轻量化:
1
轻质新材料的应用是汽车实现轻量化的关键
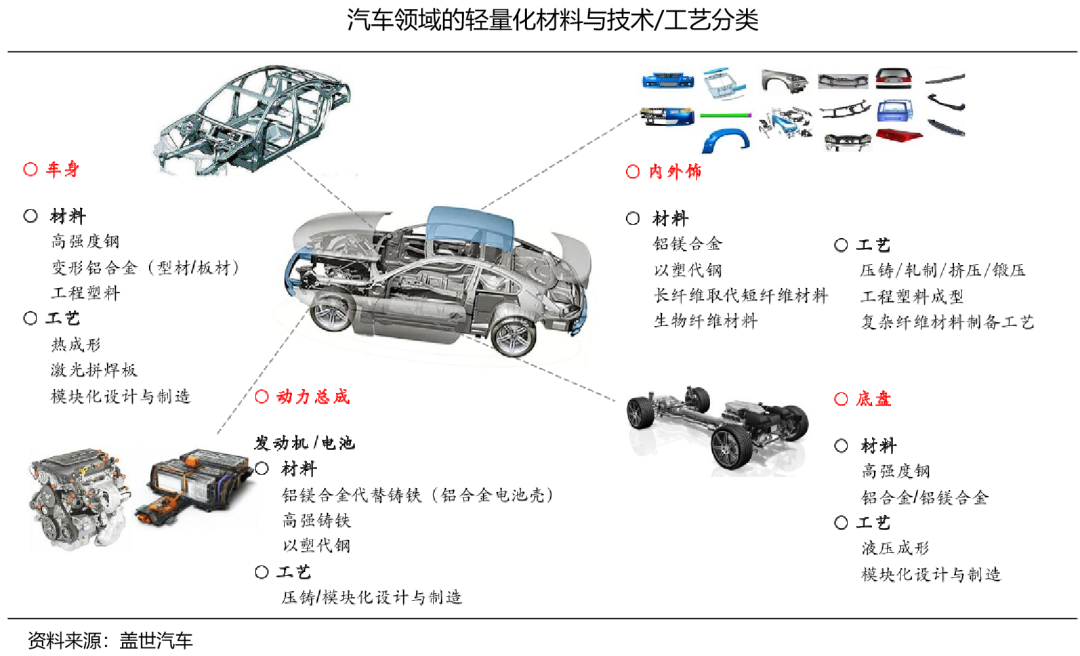
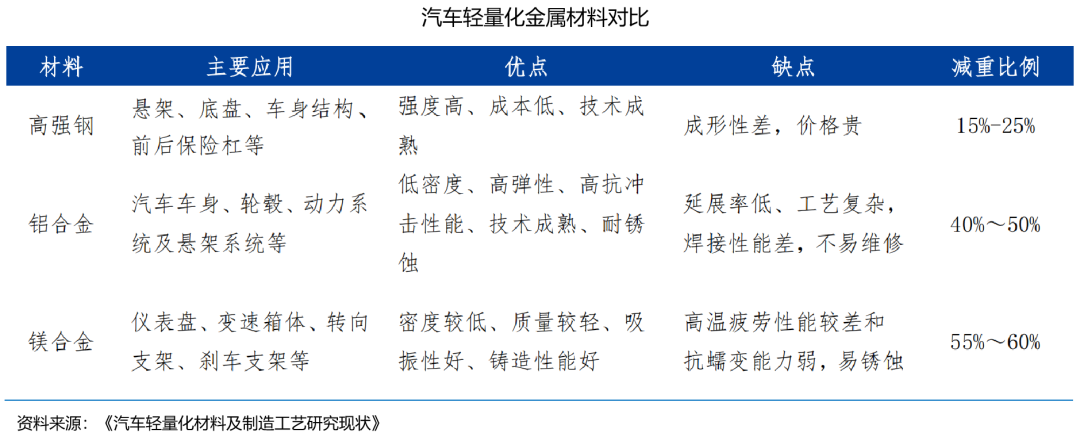
2
铝合金
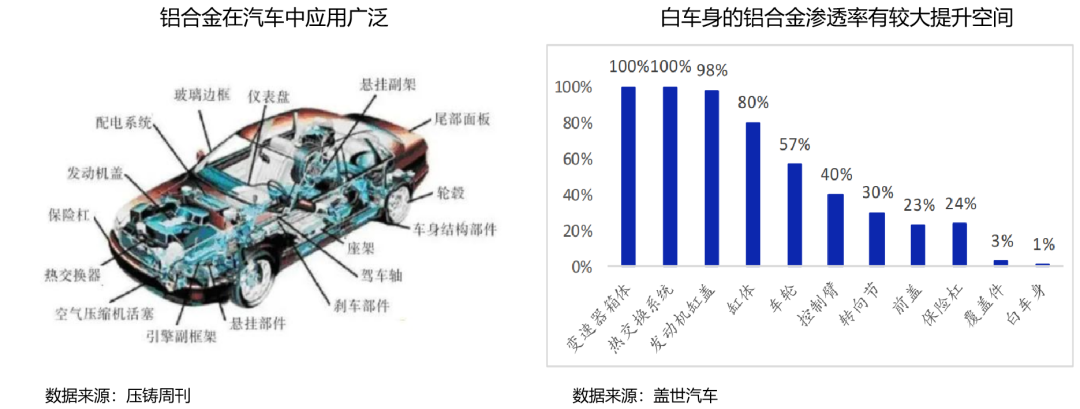
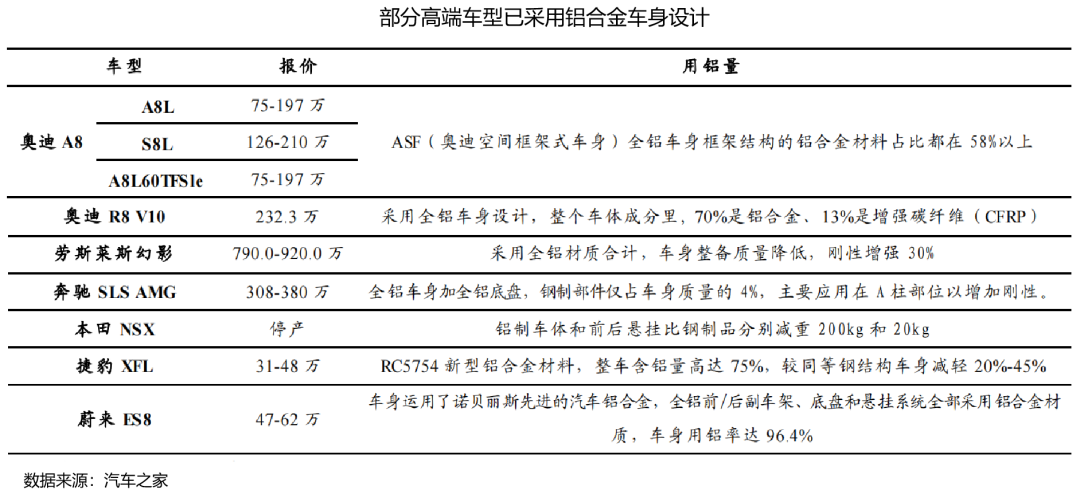
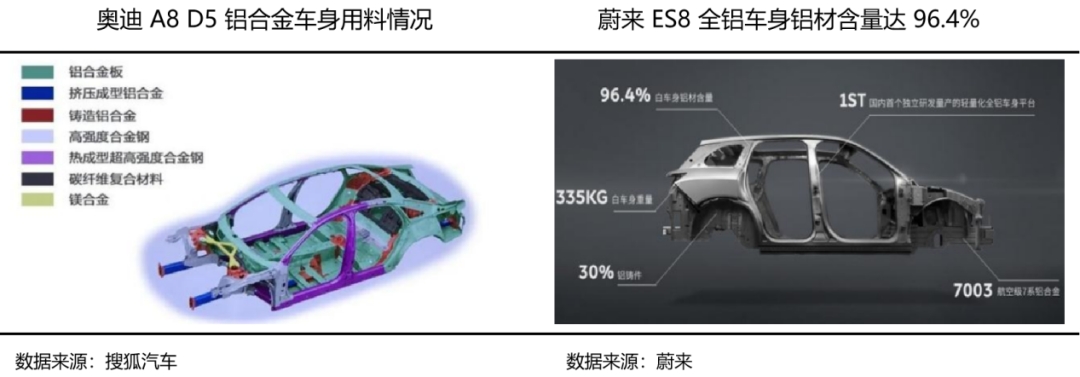
1
真空高压铸造是铝合金结构件主要制备工艺
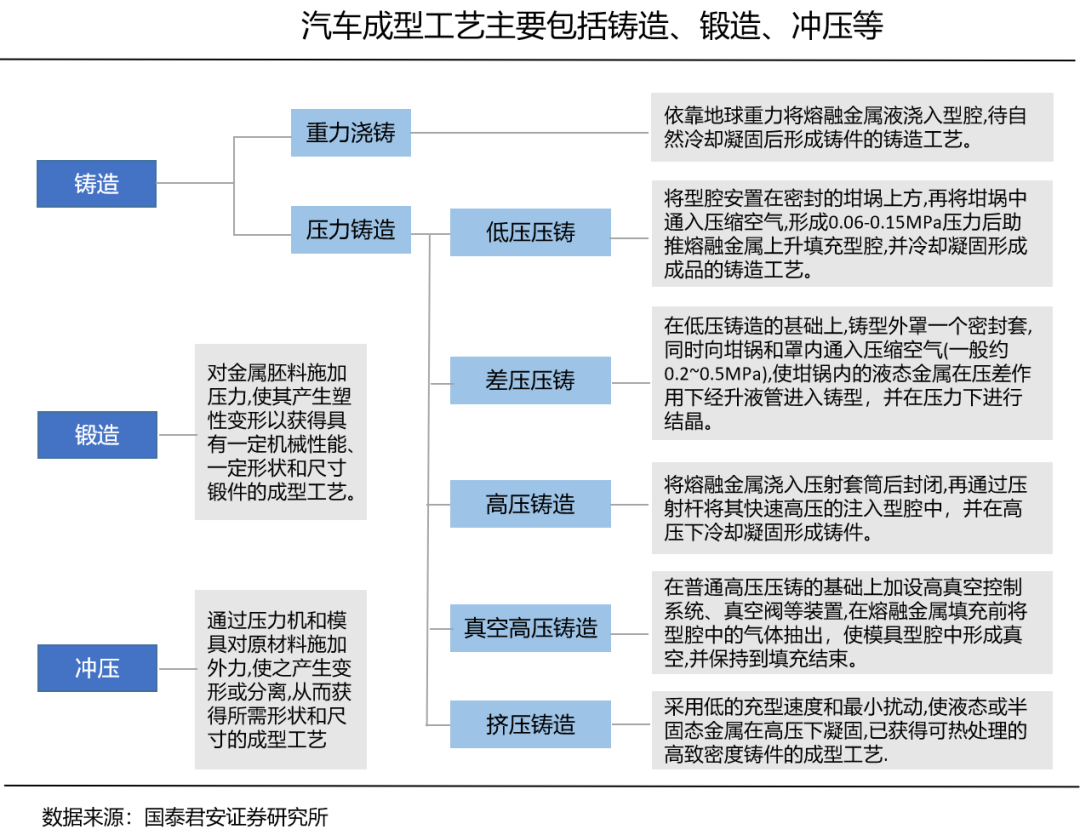
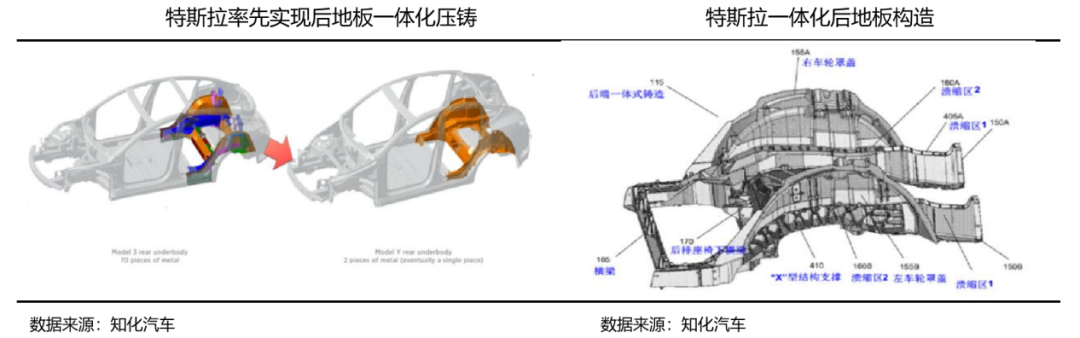
3
镁合金
相比铝合金、高强钢,镁合金密度更小,具有高比强度、比刚度和良好的铸造性、抗震减噪能力,在轻量化和一体化压铸需求发展中前景广阔。
汽车领域,镁合金主要应用在零部件上,包括壳体类与支架类零部件,包括仪表盘支架、座椅支架、显示屏支架、中控支架、方向盘、转向件等部件。
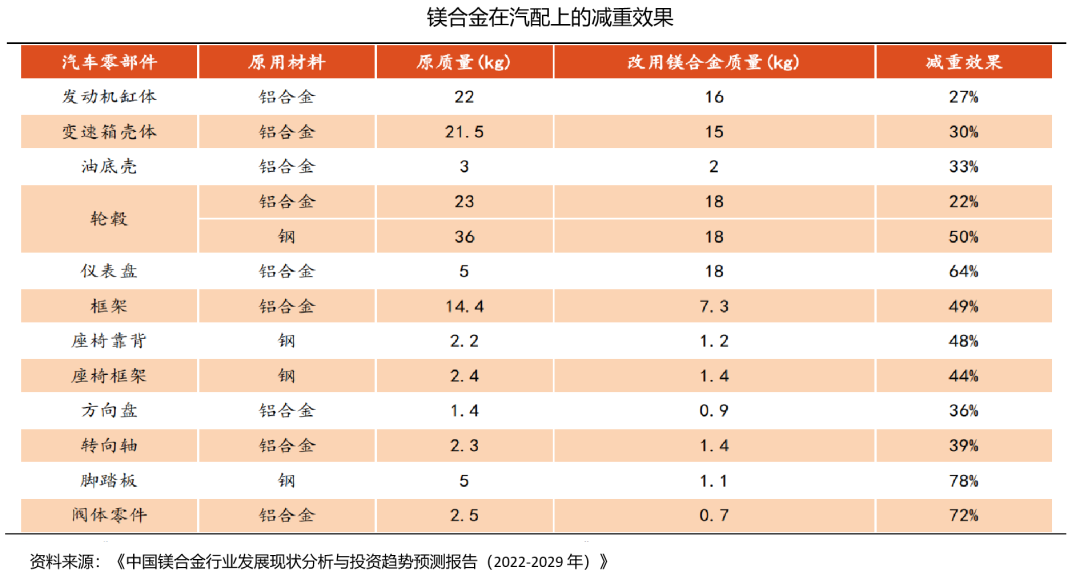
在不考虑两种金属性质差异及加工技术难度的情况下,仅从合金用量及合金价格角度分析,若镁合金与铝合金的价格比低于1.3,汽车厂商将倾向于选择镁合金作为原材料以达到单个部件原料成本最低的目标。
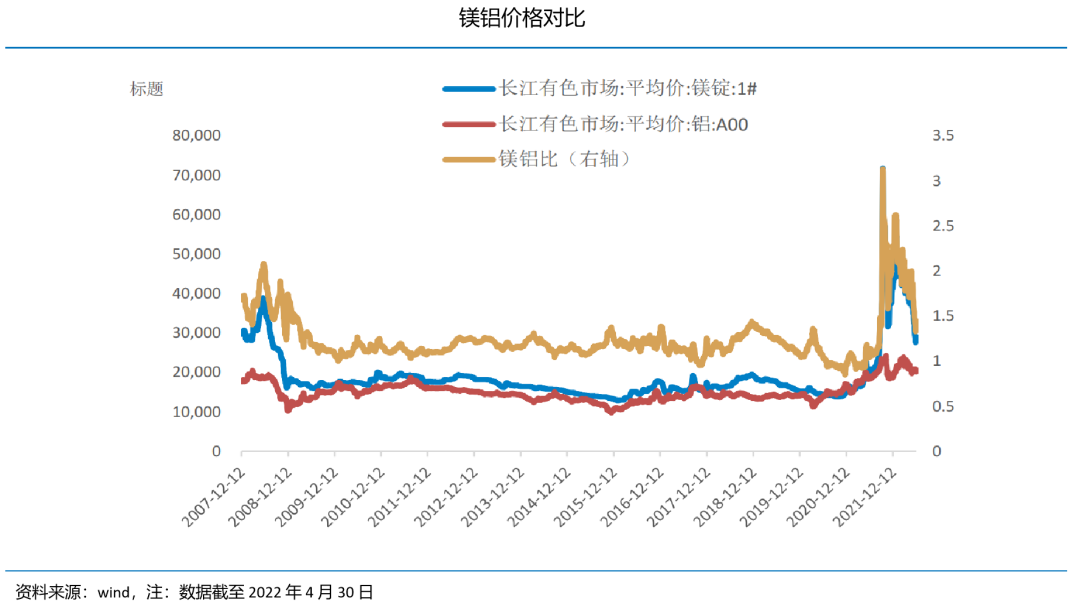
1
镁合金市场状况
2021年,全球镁锭产量为95万吨,中国镁锭产量占比达到84%,占据全球绝大部分镁锭产量,是镁市场的价格制定者。
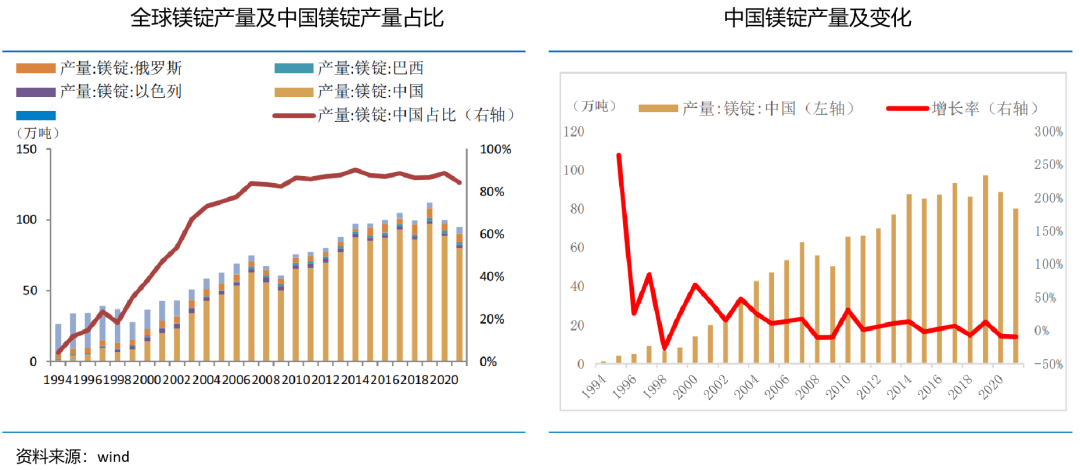
汽车领域是原镁及镁合金未来主要增长点。镁合金产品是原镁消费最具增长潜力的领域,目前约有70%应用于汽车制造,20%应用于3C产品,另外在航空航天及其他领域消费占比10%左右。
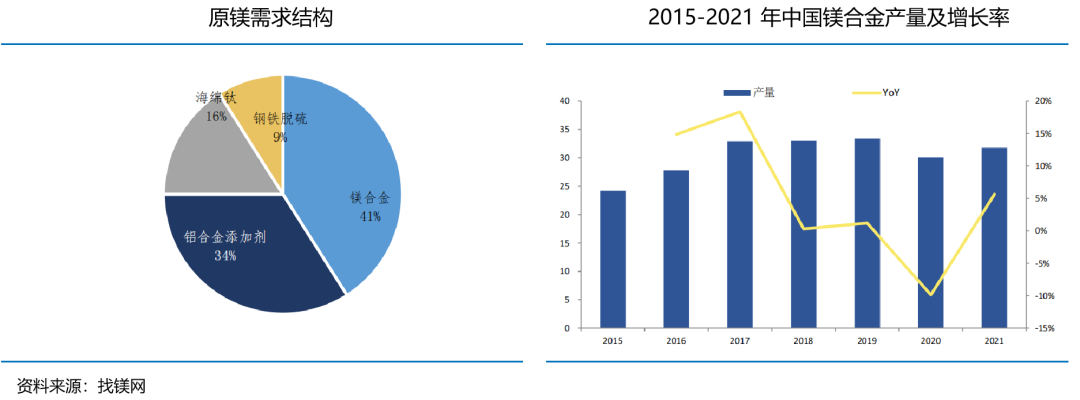
预计到2025年全球汽车领域对镁的需求量将达到112万吨。中国汽车单车用镁量较低,发展空间巨大。
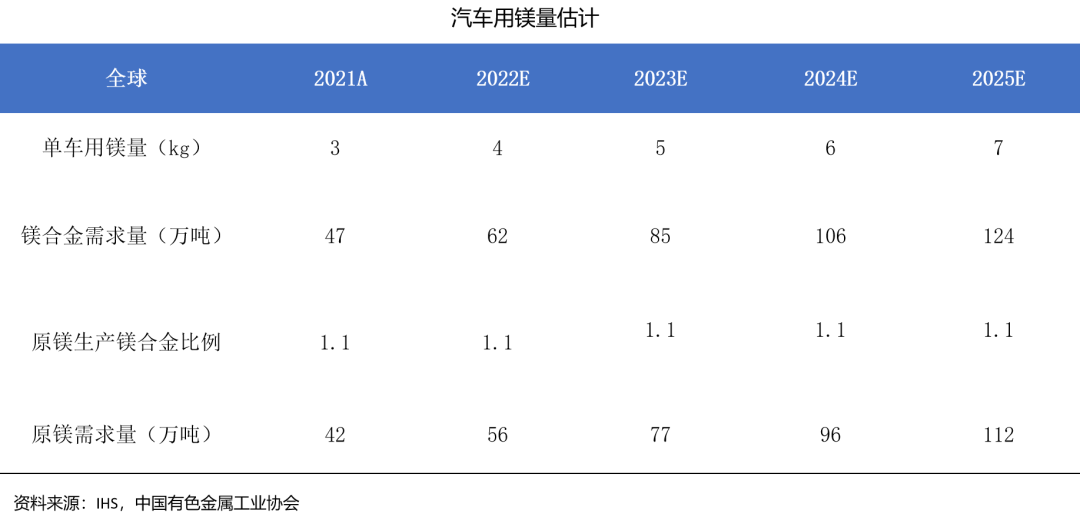
2
镁合金汽车零部件企业
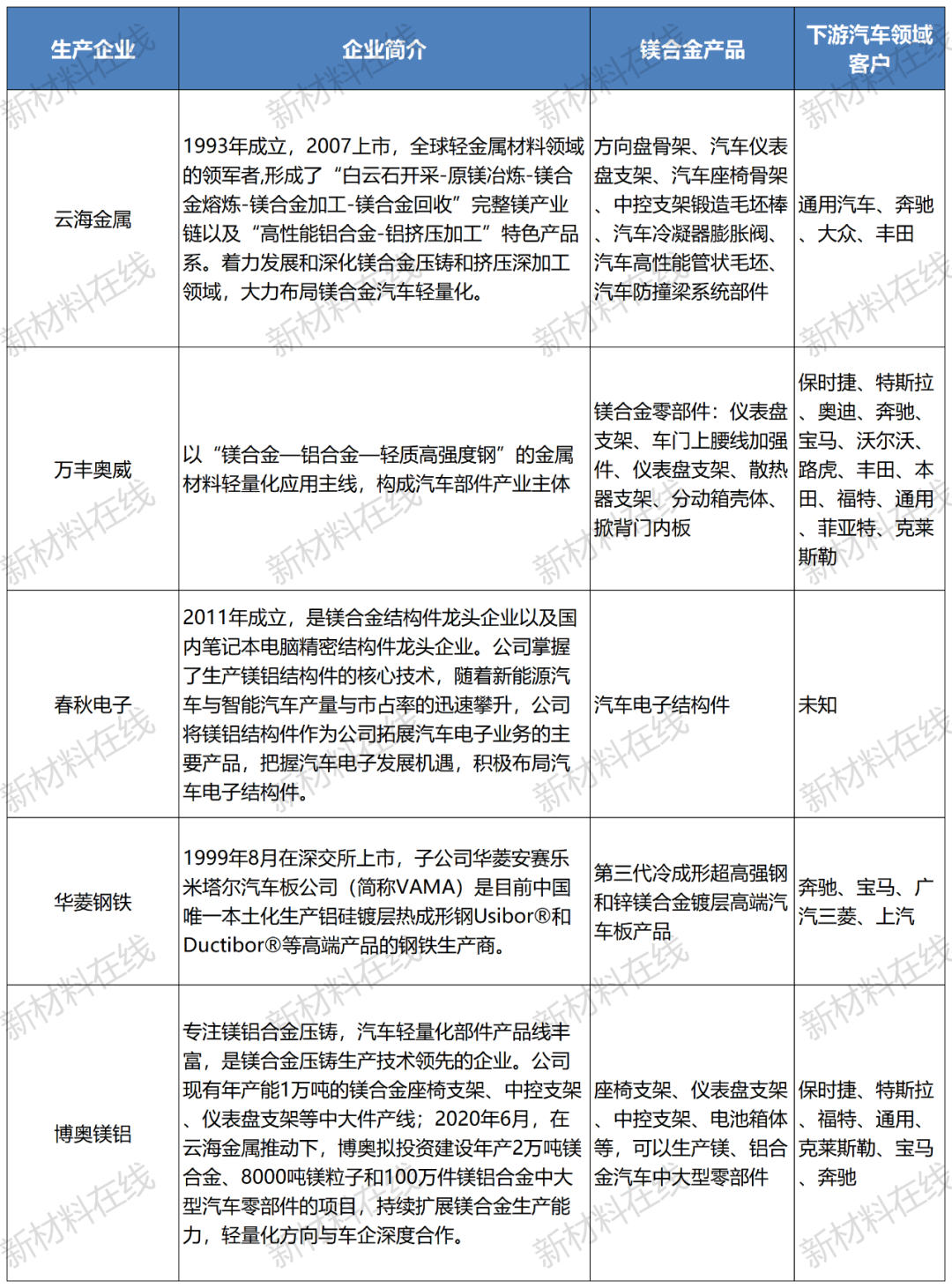
4
碳纤维
碳纤维复合材料(CFRP)的密度约为1.6g/cm³,不足钢密度的1/4,同时拥有优异的力学性能、环境耐候性、尺寸稳定性、可设计性、高吸能效率及减震性,主要应用于车身构件、刹车泵、轮毂、传动轴等部分。由于价格较高,目前主要应用在部分高端车型。
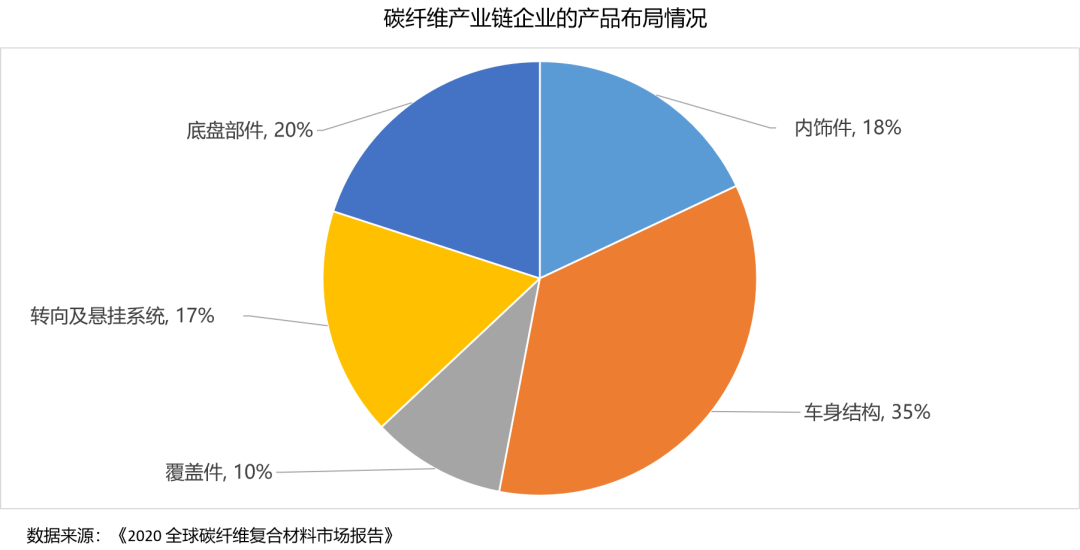
碳纤维复合材料因其材料性能优异但是成本高,最先在军工以及民航领域得到应用,根据赛奥碳纤维《2021年全球碳纤维复合材料市场报告》统计,2021年全球碳纤维的需求量为118千吨,风电叶片、航空航天以及体育休闲分别占28%、16%、14%,汽车占比8%。
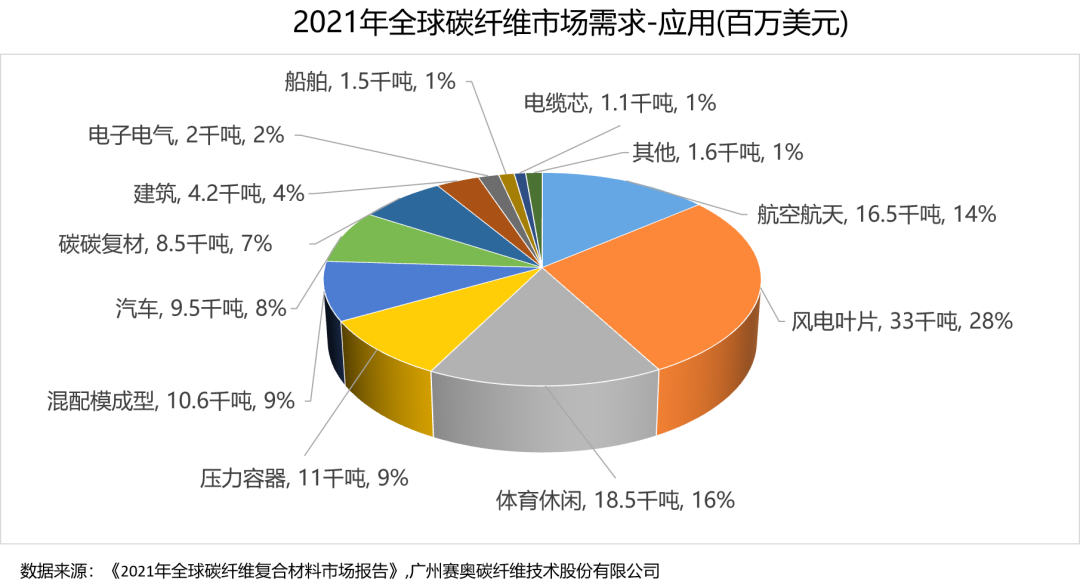
2021年全球碳纤维的需求量为11.8万吨,对比2020年的10.69万吨,同比增长10.4%。预计2025年全球碳纤维需求量将达到20万吨。在汽车行业,采用碳纤维的车型越来越多,尤其是新能源汽车,其中电池盒(尤其是底盖),有望成为碳纤维的重大需求品种。
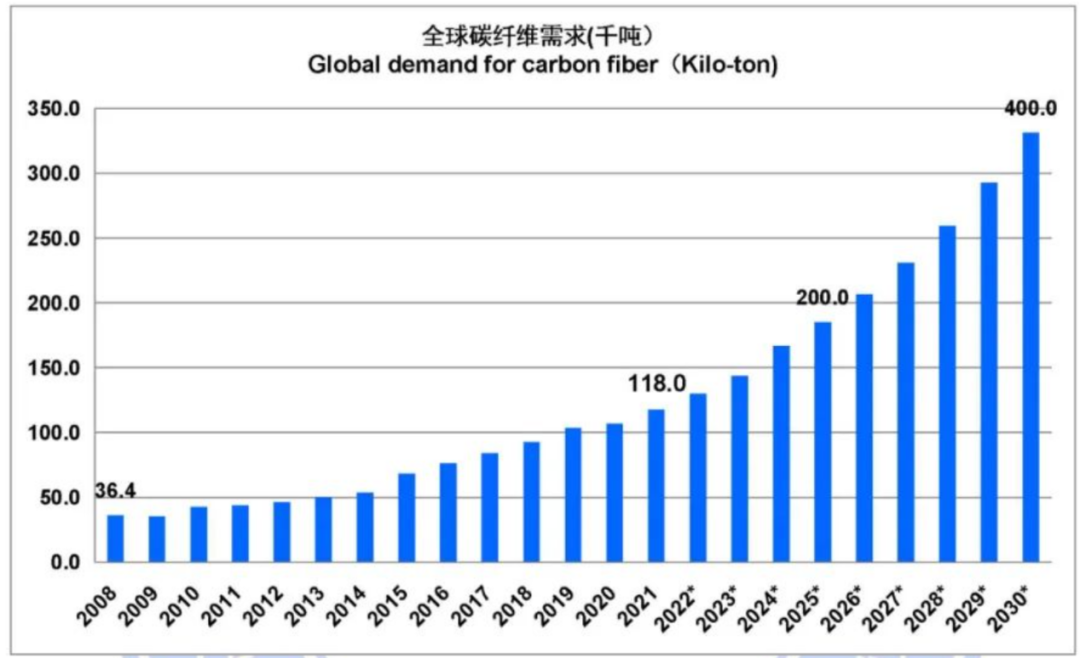
碳纤维产业链企业在产品布局上,中简科技产品主要集中在中游原丝和碳纤维环节,中复神鹰主要为上游原丝制备环节,吉林碳谷主要为大丝束原丝环节,恒神股份产业链布局相对较全,但其核心能力也主要在中游环节。
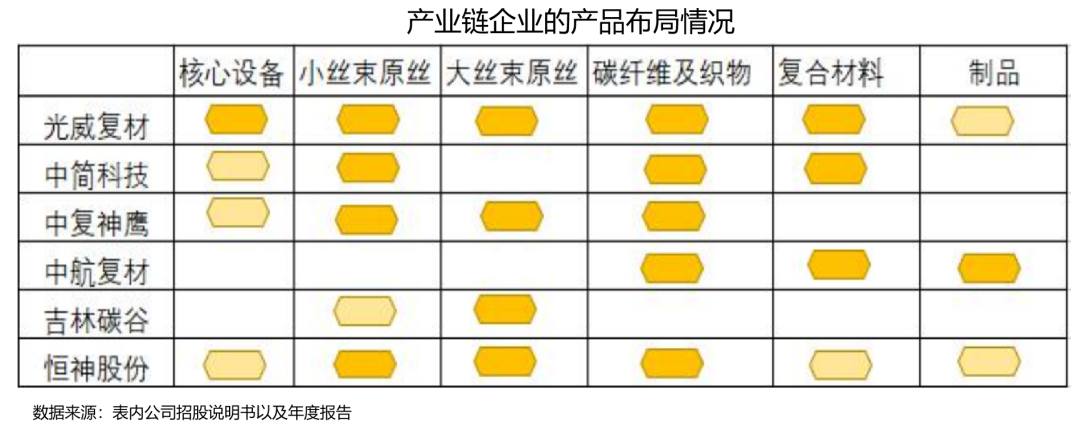
碳纤维材料在汽车工业领域的发展由高性能车逐渐走向大众汽车。20世纪50年代,世界汽车工业蓬勃发展,碳纤维布首次被用作F1的材料。80年代,碳纤维增强塑料开始在高性能豪华车中使用。进入21世纪,在宝马的引领下,碳纤维逐渐进入大众汽车领域。2014年,宝马在i3、i8纯电动汽车上大量使用碳纤维增强塑料;2015年7月,第六代宝马7系正式投产,采用碳纤维布生产车身材料,并与刚强度钢和铝完美贴合。
碳纤维在国产汽车行业尚处于起步阶段,材料成本高是碳纤维复合材料在汽车工业中大范围应用的主要障碍。2014年,奇瑞汽车与中科院宁波材料技术与工程研究所联合开发插电式混合动力汽车瑞泽7,2015年,江苏奥新全新研发的新能源汽车,之后北汽、长安、蔚来等车厂都先后研制开发了高比例CFRP的汽车,但是都处于样车或极少批量的层面。
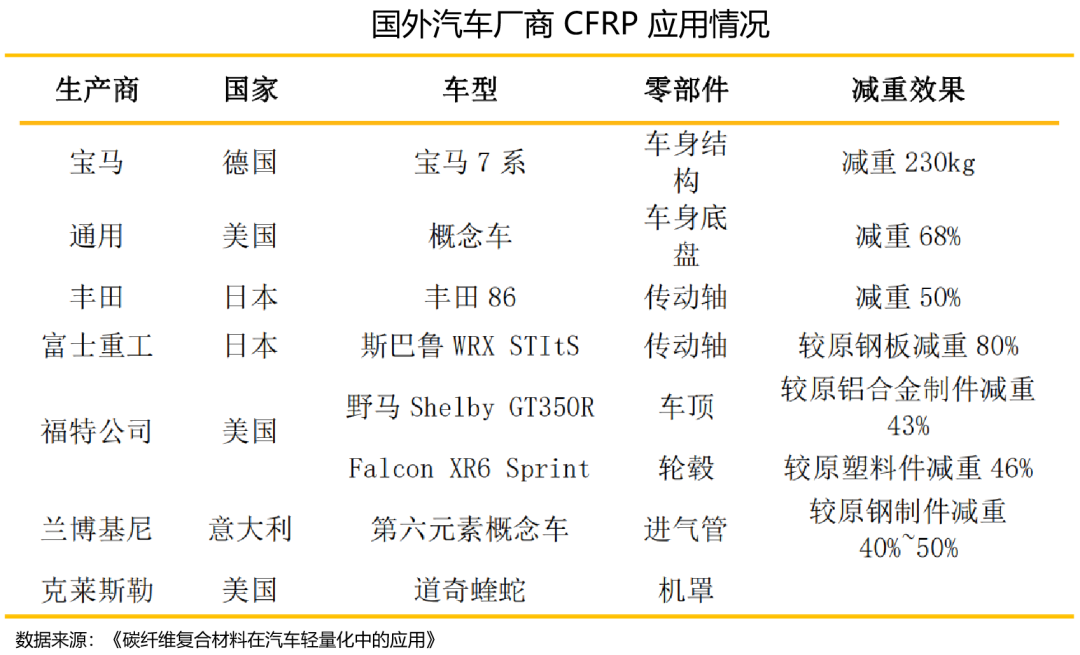
根据我国汽车轻量化技术路线图及发展目标,到2025年,在2015年基础上进一步减重20%,对轻量化材料的使用也将逐步由高强度钢、铝合金逐步扩大至镁合金、碳纤维等,最终实现碳纤维复合材料混合车身及碳纤维零部件的大范围应用。根据路线图,至2025年,碳纤维复合材料用量将占到车重的5%,市场规模接近600亿元。
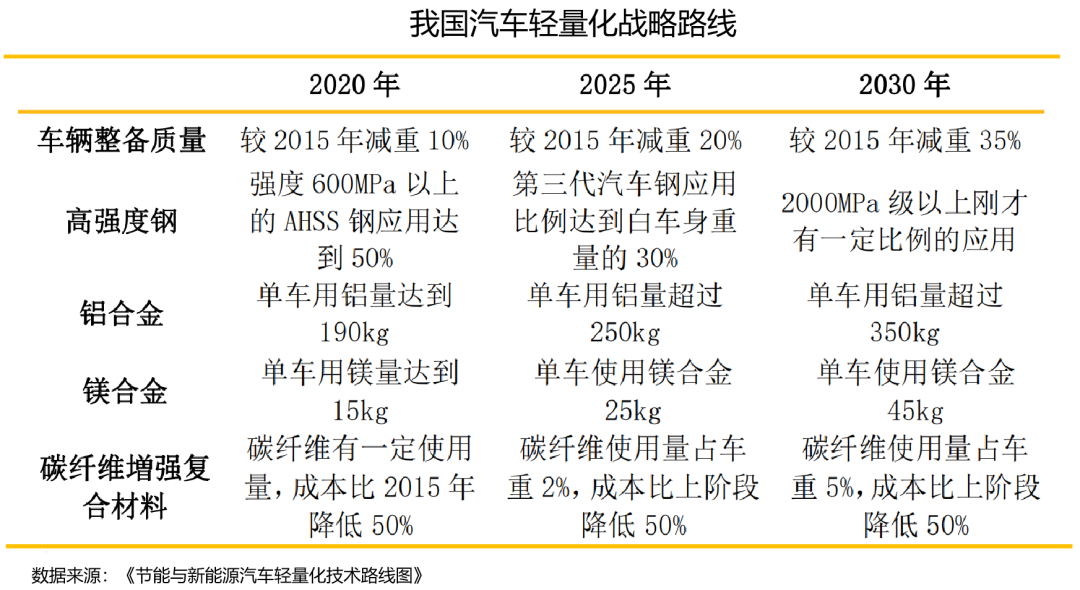
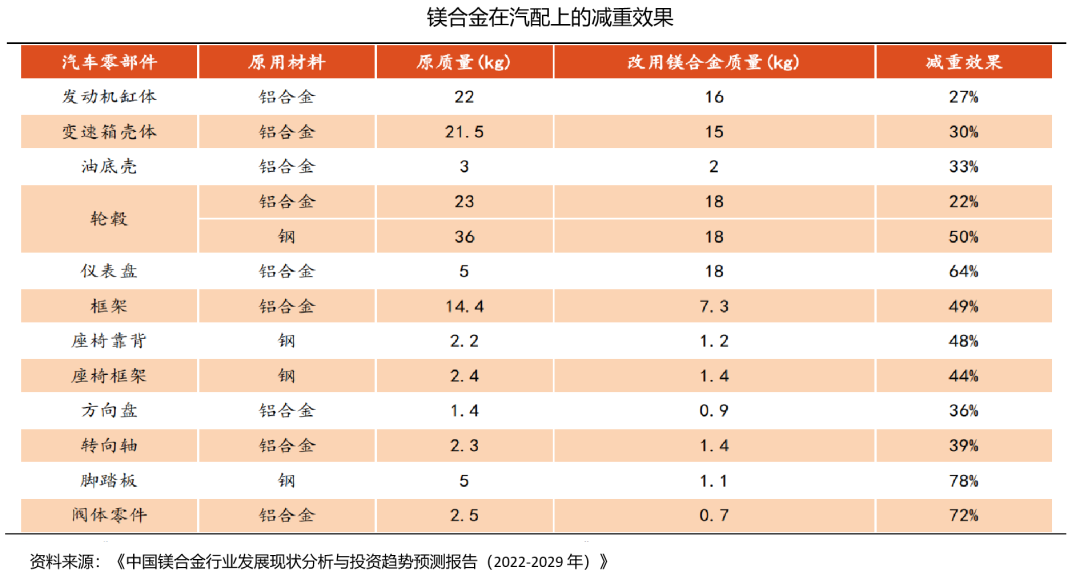
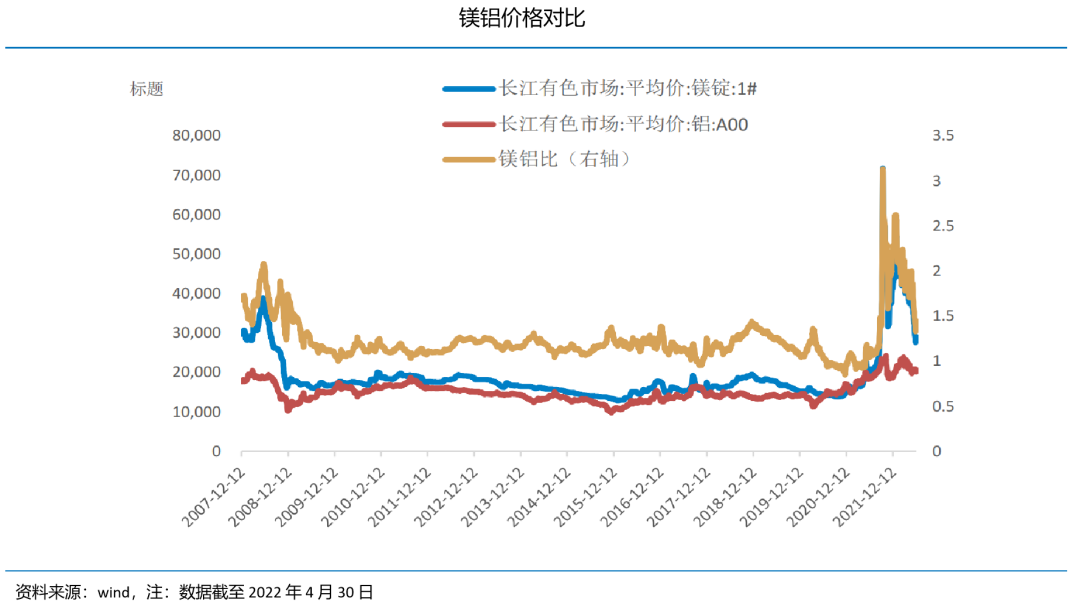
1
镁合金市场状况
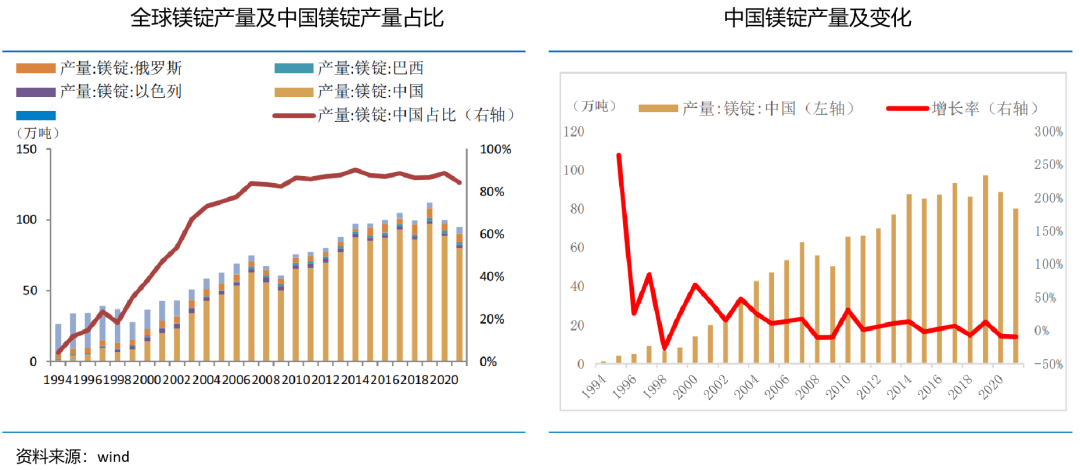
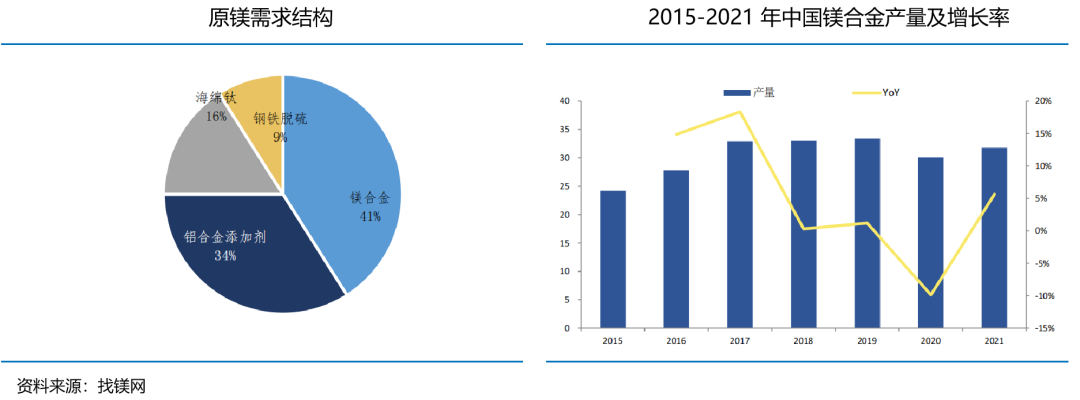
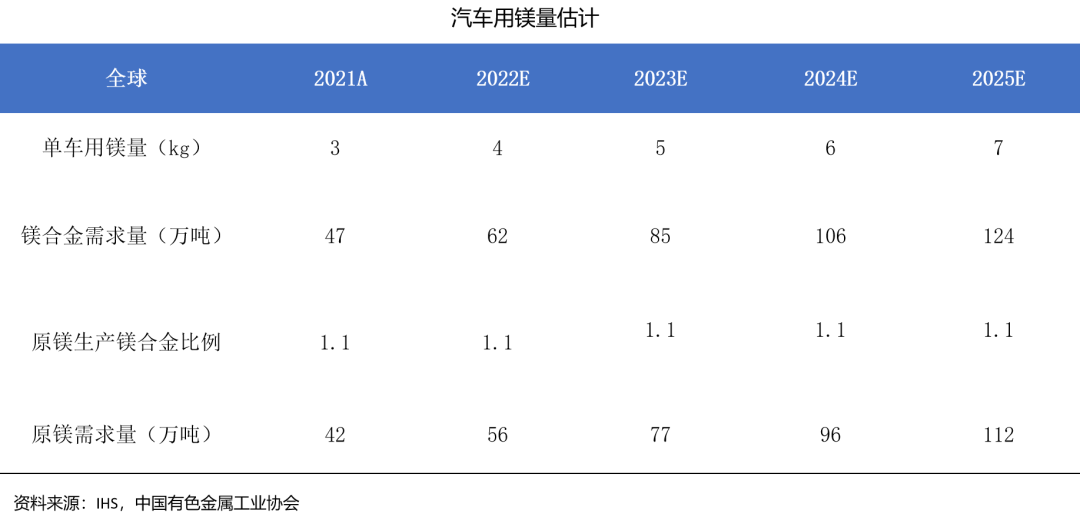
2
镁合金汽车零部件企业
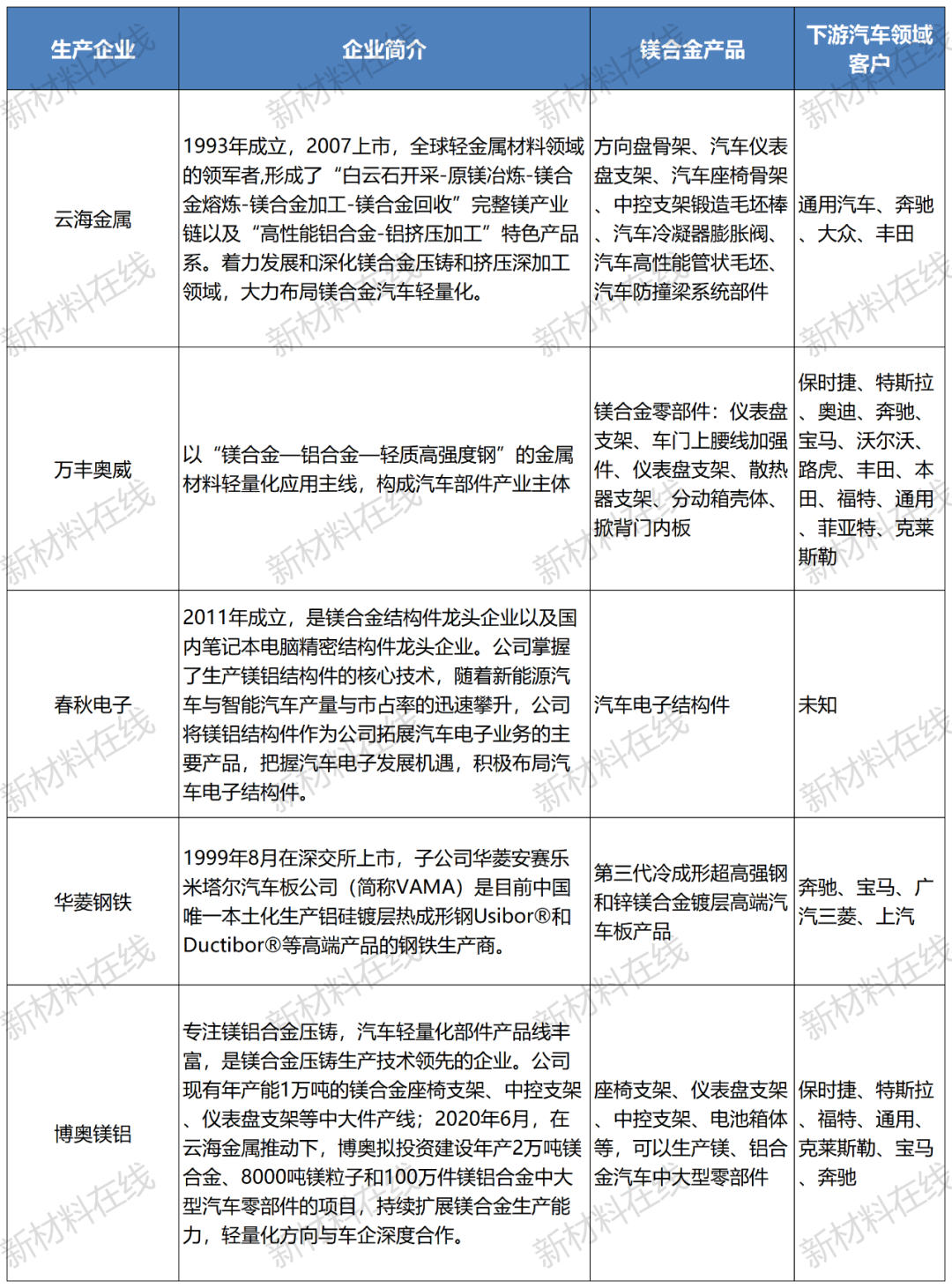
4
碳纤维
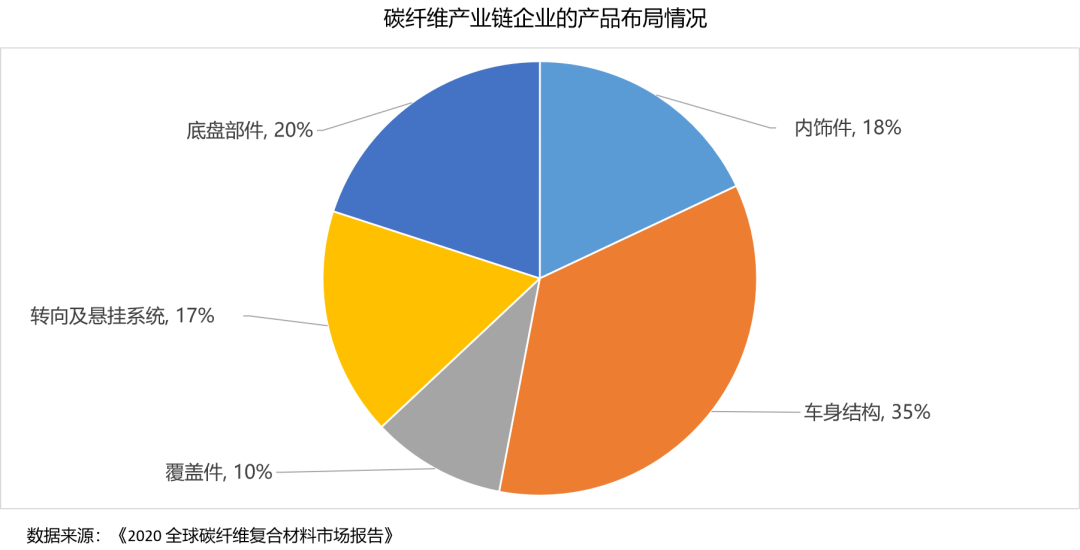
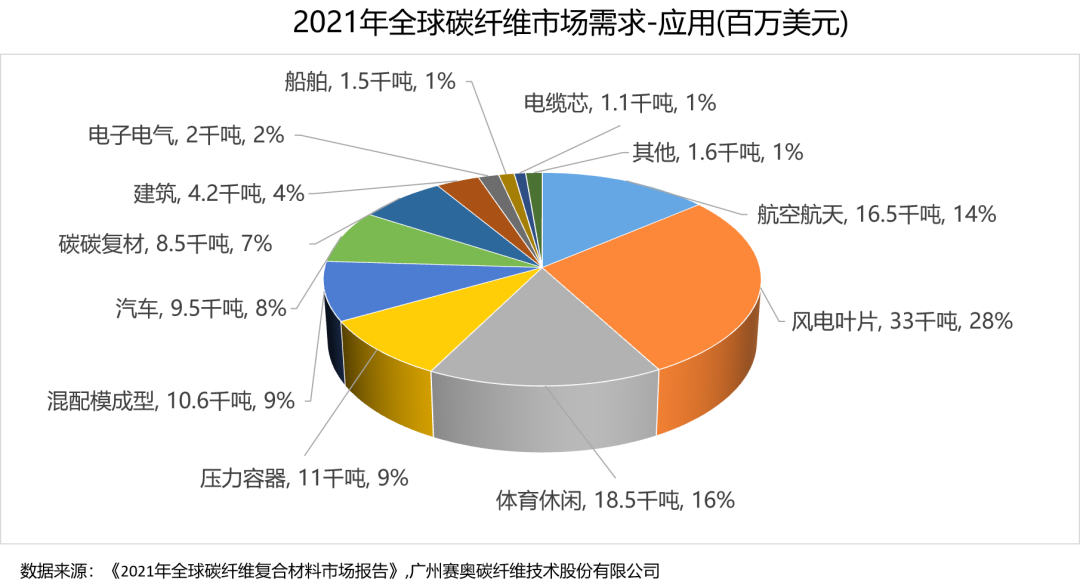
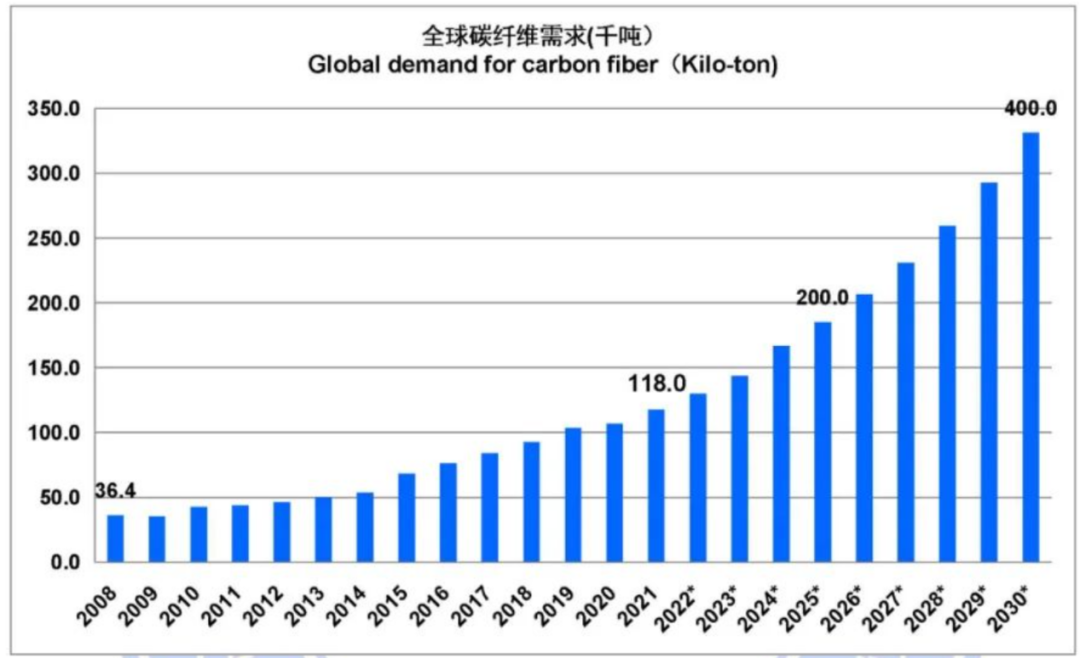
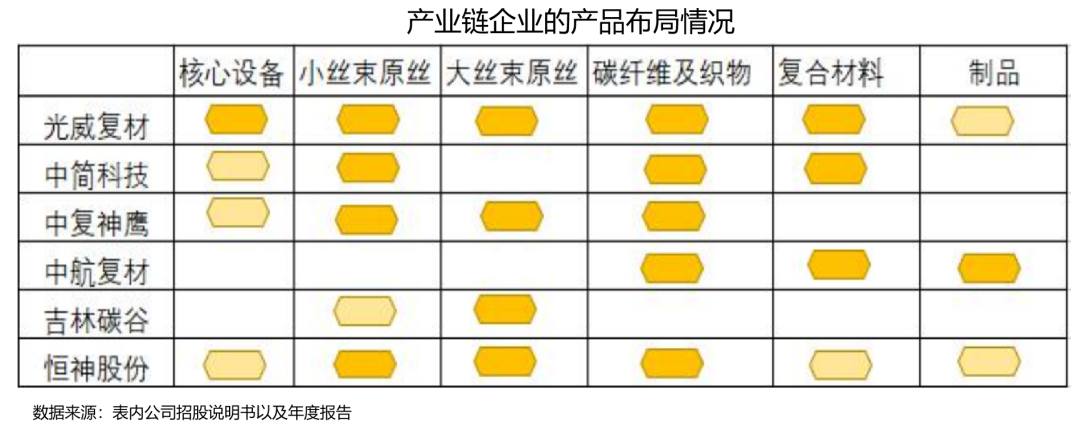
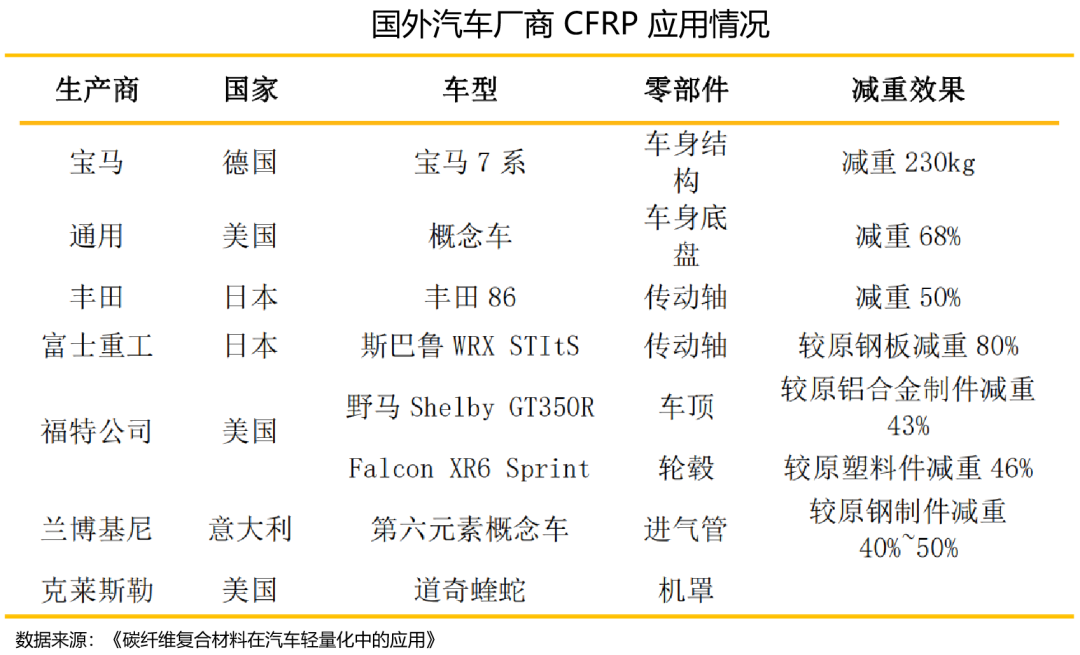
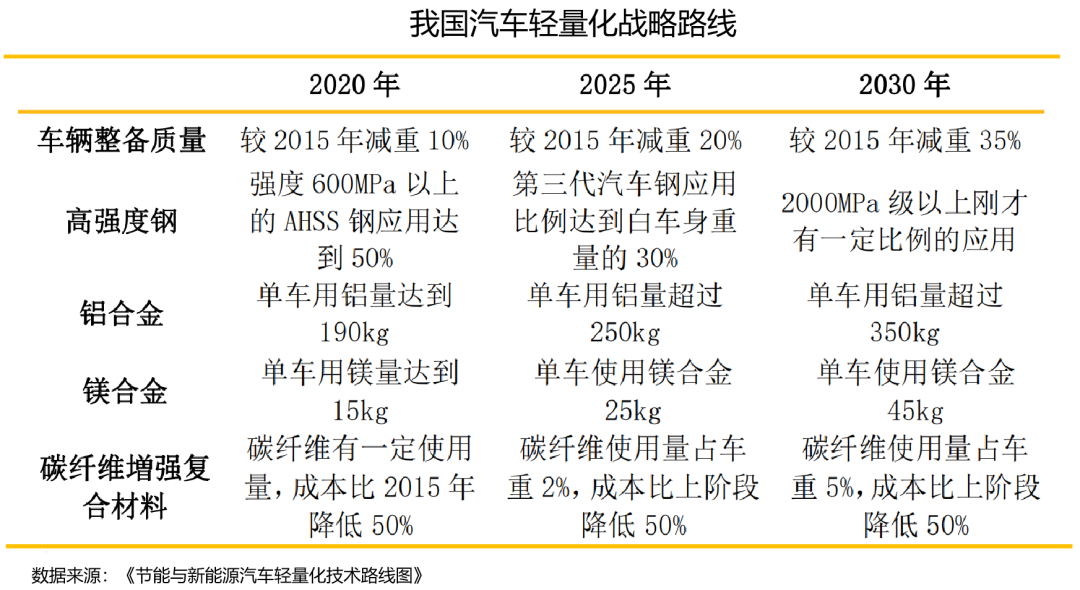
[ 新闻来源:新材料在线,更多精彩资讯请下载icspec App。如对本稿件有异议,请联系微信客服specltkj]
存入云盘 收藏
举报
全部评论
暂无评论哦,快来评论一下吧!
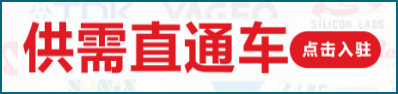
新材料在线
开创IC领域,共创美好未来!
查看更多
相关文章
科创板半导体并购潮:政策驱动下的产业整合新趋势
2025-06-11
Meta下一代VR设备将采用轻量化设计,预计2026年发布
2025-06-04
三星或与中国企业合作,以降低OLED面板材料成本
2025-06-16
手机CIS市场生变:高性价比成新趋势
1 天前
混合键合技术将成AI芯片发展新趋势
2025-05-12
热门搜索
高通进军数据中心市场
海光信息合并中科曙光
华为
台积电
中芯国际
联发科
高通
英特尔
芯片