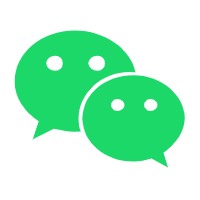
今年SEMICONChina展会的热闹程度是可以用“接踵摩肩”这个词来形容的。可能从半导体制造与封测上游设备的角度,能探访尖端工艺的机会又比以往更多了——不少很少在中国国内露面的企业,这次也都来了,比如会上我们探访的ERS、Manz等。
这次另一家我们接触到的上游设备/装备企业,是KS(KulickeSoffa,库力索法)。这家公司在半导体封装、显示面板制造领域都有对应的产品。其实我们感觉KS在SEMICONChina展示的新品,包括新发布的POWERCOMM和POWERNEXX球焊机,以及因为前不久刚刚收购AdvancedJetAutomation展示的点胶设备等等,都属于其传统强项,不及其先进封装与制造技术有趣。
KulickeSoffa执行副总裁兼总经理张赞彬
当然这些传统技术还是KS营收的主力,毕竟量很大。KulickeSoffa执行副总裁兼总经理张赞彬在媒体会上特别提到,传统封装用的像是打线机仍然是重要的营收来源,包括国内封测厂对这类设备量的需求也很大。
不过我们主要还是期望谈谈KS的尖端技术,即便像在先进封装领域,中国大陆的设备用量仍然不大,却也能让我们更进一步地了解,对于半导体先进封装,以及显示面板制造的尖端技术,从上游设备厂商的角度,已经走到了哪里。
这篇文章我们谈一谈miniLED、microLED显示技术,和KS在这个领域都在做什么。另外一篇有关KS先进封装fluxlessTCB技术的文章点这里查看。
miniLED与microLED的难点:巨量转移
关注显示行业的同学,对miniLED、microLED应该都不陌生。尤其苹果在iPad、MacBookPro设备上开始用miniLED背光,自然会带动显示行业不小的震动。2021年,我们探讨miniLED和microLED的技术文章也写了不少,包括iPad的mini LED光晕效应存在的原因,micro LED的未来展望等。
简单来说,将原本传统LCD的背光LED芯片做小——当小到一定程度后,就可以叫做miniLED。比如2021年iPadPro12.9"的屏幕背光由10000颗LED构成,这样的屏幕就可以叫做miniLED屏;当显示芯片进一步缩小,通常<50μm时,达到像素级别,就可以叫做microLED了。
一般从像素的角度来看,如果每一颗LED芯片对应于一个像素,传统液晶结构随即被推翻——这样的屏幕都可以叫做microLED屏幕。从传统LCD到miniLED/microLED的转向,可以近似看做背光分区的越来越多,一直分区到每个像素都有单独的分区。则很显然显示对比度、黑位等的控制,加上面板结构变化所致的效率提升,都令其性能、功耗显著领先于LCD。
显示行业普遍认为microLED是有巨大潜力取代OLED技术的,因为其microLED屏幕的亮度及寿命,都是OLED无法比拟的。
但现阶段无论miniLED,还是microLED,最大的问题都在成本控制上。过去的技术文章里,我们已经谈到microLED发展的几个重大技术挑战,首先就是巨量转移(masstransfer);随后还有包括microLED较低的发光效率(EQE)、从系统角度来看需要选择不同阶段的工艺技术,以及背板基板的制造、RGB三色实施方案等。
其中被谈得最多的还是巨量转移——也就是在miniLED/microLED制造过程中,将LED芯片从原wafer迁移到背板上的过程。当代显示面板分辨率正显著提升——4K分辨率就超过了800万个像素,每个像素又有RGB三个子像素,即一块4K分辨率的面板,若基于microLED,就需要将超过2400万颗LED做转移。转移效率、对齐精度、良率等相关工艺难度都非常大。
“现在最新要发展的direct-litLED,这颗0406——也就是89x225μm尺寸的芯片用作背光——背光的数量相比之前就会增加。”张赞彬说,“目前我们在开发的是0305(75x125μm)——像这样整排的,我们称其为full-arrayLED。”
所以“转移最大的问题在于数量多,传统方案速度很慢”。尤其到microLED,“尺寸小到38x54μm,然后在开发中的24x40μm,甚至<10μm”,“转移的速度是必须要增加的”,因为速度的增加就意味着成本的降低。
如果用激光转移
我们此前提过,巨量转移的方法不止一种。张赞彬在媒体会上说,PDMS(polydimethylsiloxane)stamp压印,和激光转移(lasertransfer)是两种常见的方法。“KS选择了激光转移的方法”,包括面向miniLED和microLED。
下面这张图列出了KS针对不同尺寸的LED,采用的不同方案。“>200μm的芯片,我们用传统SMT贴片机(也就是此前讨论最多的pickandplace)的方法,因为速度基本是可以接受的——毕竟(LED芯片)数量不会很多,尺寸也大,用传统方法就可以了。”
“而在200-50μm的尺寸上,是从2019年开始,我们就有Pixalux——也就是探针的方法,机械式地去做转移。”探针是从wafer背面将芯片压下去。这张图中列出这一尺寸的转移,也可以用到名为Luminex的设备,“我们的第二代Luminex,激光转移的方法”,未来也会针对<50μm的microLED芯片转移,“用激光的方法,可以处理的尺寸会更小”。
张赞彬说转移的良率非常重要,“我们目前能够达到的良率是99.999%,5个9。要达到这样的良率是因为人眼对于显示面板的要求很高,哪怕一个坏点都会看到。”而传统的“stamping印压的方法会将好的、不良的芯片一起转移过来”,这就涉及到了repair”,“一小颗出了问题,就需要回到那个位置,把它挑出来,再放入一颗——这个过程很难。repair本身的速度就非常慢”,也就相应地影响到了成本。
所谓的激光转移方法,是用激光头(bondheadwithlaser)通过激光将LED芯片移到基板上,基板再转到面板。KS前两年收购了一家名为Liteq的公司,获得了更完整的激光转移的相关技术和专利。“这个方法需要用到某种膜,激光打到膜上,产生blister气泡——气泡将芯片推下去——这是我们的一项专利。”(如下图)
“芯片越薄、越小,用传统的机械方法,操作的困难就越大——光是探针就需要磨得很尖很小;而激光方法能够处理尺寸很小的芯片,并且达到相应的精度,处理的数量还很多。”
激光转移的另一个重要价值就是速度快。张赞彬说对于0509这个尺寸而言,大约10μs的时间就让芯片到接触DCM(diecatchingmaterial)。则相应的,激光转移方法达成了显著更快的转移速度。
相比于传统pickandplace只能达到每秒10-20颗的速度,KS2019年开发的Pixalux——前文提到的探针方法令速率超过了50Hz。而最新的Luminex——即激光转移方法最快可以达成10000Hz,“激光扫描的速度很快,因为完全没有碰到wafer”。
据说如果用15Hz的速度去造主流分辨率需求的microLED电视,这个过程可能需要1周,与此同时电视的最终售价可能高达20万美金。“良率差、速度慢、成本就高。这也是microLED面临最大的挑战。”
但似乎即便激光转移能够将速度提升到10000Hz,张赞彬仍在答记者问时说:“我觉得1万颗1秒还是不够快,我们的目标是要做到100万1秒。做得到吗?我们还是在不断努力的。”“就像很多年前LCD电视都要1万美金,现在便宜多了。”
“其实miniLED的成本过去几年已经降了很多了。从材料、芯片,到转移设备等等,越来越多玩家进入。”所以像苹果、三星这样的高端市场玩家在平板、电视之类的设备上应用miniLED技术也就不足为奇。
这项技术中,KS的主要专利就集中在激光、DRL和DCM上。“ChiponBoard和PackageonBoard这两种方法我们都提供。现在考虑做薄的需求,COB会比较多。”
从工艺角度来看,要达成更小的pixelpitch、更高的精度和准确度,“激光方法未来可以往下走的,探针方法就存在限制——激光方法未来2-3年都会有发展空间。”
从更实际的角度来说,Luminex解决方案在面板制造的位置,处在LED芯片的wafer切割以后,进行diesortingmixing、re-pitching和diebonding这几个步骤。现阶段Luminex支持的最小尺寸如下图所示(0305,75x125μm);还在开发<50μm即microLED更小尺寸的支持。“未来8K电视、AR/VR眼镜,智能手表都会进入到<10μm的范围”。
“以后眼镜最低就要做到8K分辨率。”在谈未来microLED的应用时,张赞彬说,“我觉得第一步是眼镜,因为屏幕小。尺寸小良率就会比较高。”电视则要稍晚一些。
成本、良率和未来
不过有一个问题仍然是不可回避的,就是成本——前面谈到的这些,包括更快的转移速度、更高的良率都促成了可变成本的降低;但半导体行业某一类技术前期发展的成本大头往往是CapEx固定成本。
“设备价格可能会贵,因为用的是激光。”张赞彬谈到,“但我们的性价比是可以高出3-5倍的。我们这样一台(激光转移)设备,从速度上可以取代4-5台传统贴片机。而且一台设备还节省了占地面积。如果说厂房里10台设备就够了的话,那么传统设备可能需要100台。”
“现在microLED这边(Φ=~8um),我们可以达到99.999%的良率——我觉得这是市场的一个标准。就是厂商要赚钱的话,至少要99.9%,三个9。我们将来的目标是6个9,也就相当于99.9%的1000倍。那么成本会降到很低。”如前文所述,“因为每次发生不良,repaircost会很高。”“未来达到6个9,行业是要往这个方向发展。”“良率高、速度快,成本就会降低。”
张赞彬特别提到了现阶段在开发中的microLED解决方案,diesize是在20x40μm,预计精度要做到2μm3sigma——也就是偏差控制在2μm。“未来希望能把精度做到1μm,因为误差越大,良率也越差。”张赞彬给出的PPT上提到了多die转移的具体目标是每小时1亿片——可大致给出一个基本概念。
1亿片/小时(>100KK/hour)是激光转移方法现在能够达到的水平;PDMS转移高吞吐量的大致水平是最高500KK/hour。不过张赞彬强调了,选择激光转移方法,是“当芯片越来越小,我们还有空间往下走”。这张PPT总结性列出了激光转移与PDMS转移的优劣对比。
“现在还是用传统方法比较多,因为就成本角度大家都能接受。”“现在市场上大部分的方案还是基于机械的。每个行业的新技术都需要一个时间去验收——虽然方法是对的,但可能验收的时间很长。”张赞彬在总结时说,“机械方法已经发展了二三十年了,也正越做越快、越小。现在要转向激光方法,行业还是需要时间。”
“最近我参加的研讨会,大家都在说microLED的各种技术挑战。我觉得我们一定会达到这个目标,只是需要一点时间。”
暂无评论哦,快来评论一下吧!
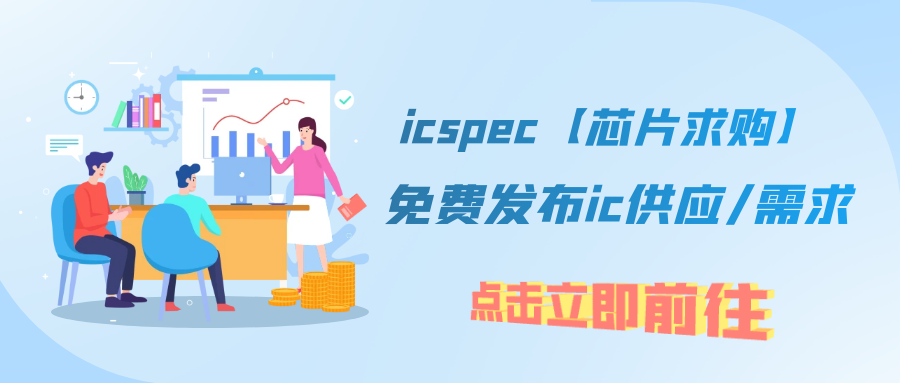