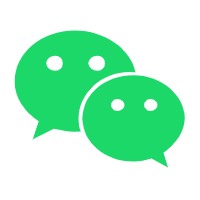
使用化学机械抛光(CMP)方法对碳化硅晶片进行了超精密抛光试验,探究了滴液速率、抛光头转 速、抛光压力、抛光时长及晶片吸附方式等工艺参数对晶片表面粗糙度的影响,并对工艺参数进行了优化,最终 得到了表面粗糙度低于0.1 nm的原子级光滑碳化硅晶片。
与传统半导体相比,单晶碳化硅作为新型半导体 材料,具有禁带宽度大(3.3 eV)、击穿电场高(0.8~ 3.0 MV/cm)、热导率高(3.0~4.9 W·cm-1K-1)、饱 和电子漂移速率高(2.0×107 cm/s)等突出优点,可 满足在高频高功率电子器件方面的需求,传统半导 体无法代替。因此,单晶碳化硅在电子元器件的应 用成为未来发展的必然趋势,而碳化硅晶片的生长 技术又是器件制作的前提,如何将碳化硅晶锭制作 成符合要求的碳化硅晶片就成为了关键环节。
单晶碳化硅具有超高硬度,其莫氏硬度高达 9.5,加工难度十分巨大。碳化硅具有极其稳定的化 学性质,在常温下不与任何已知的强酸或强碱等化 学试剂发生反应,且碳化硅的压缩强度远大于其弯 曲强度,材料具有较大的硬脆性,导致碳化硅加工难度巨大。目前国际上部分发达国家已具有成熟的 碳化硅单晶衬底的制备技术,其中美国碳化硅单晶 衬底技术最为成熟,垄断了国际上80%的市场,而国 内则处于起步状态,距离国际顶尖水准还有较大差 距,因此打破国际技术垄断,制备超光滑的碳化硅衬底晶片,具有十分重要的意义。
为得到表面超光滑的碳化硅衬底晶片,用改造 后的设备对碳化硅晶片进行了超精密抛光试验,得 到了表面粗糙度低于0.1 nm的超光滑碳化硅衬底晶 片,并探讨了晶片的粘贴方式、抛光压力、抛光时 长等参数对晶片表面粗糙度的影响。
碳化硅单晶衬底的制作需要经过切割、研磨、 抛光等一系列工艺,最终得到超光滑的碳化硅衬底晶片。其中,抛光又分为粗抛和精抛:粗抛的目的 是将衬底表面粗糙度加工至纳米级别;精抛是碳化 硅衬底晶片制作的最后一步工艺,其直接关系到加 工之后的衬底能否投入生产。精抛的目的是进一步 改善碳化硅衬底的表面质量,得到超光滑表面质量 的晶片,通常要求表面粗糙度低于0.2 nm以下。
获得超光滑表面碳化硅晶片的抛光方式中,包 括电化学抛光(ECMP)、摩擦化学抛光(TCP)、化 学机械抛光(CMP)等,其中化学机械抛光将化学 抛光技术和机械抛光技术相结合,是当前国际上公 认,可实现全局平坦化和超光滑无损伤纳米级表面 的加工方式。试验中使用自主研发的设备对碳化硅晶片进 行CMP,如图1所示。抛光盘使用质地较硬的铸铁 材质,具有良好面形,表面粘贴的抛光布使用无纺 布,抛光头下面带有真空吸附功能,通过调节真空 吸附压力可以将陶瓷盘牢牢吸附住,此外,设备还 具有滴液调节及搅拌功能,可以根据需求对抛光液 的进给速率进行调节和搅拌。
抛光液采用粒径在100~300 nm范围内的SiO2磨粒 作为抛光介质,使用KMnO4作为催化剂和氧化剂, 同时加入KOH溶液用来调节抛光液的PH值使其呈碱 性,其反应原理如图2所示,抛光液中SiC与氢氧基进 行化学反应,在氧化剂及催化剂作用下,SiC表面生 成SiO2改质层,在磨粒机械作用下去除。
抛光时间设定为6~12 h不等,抛光压力设定为 200~260 N,抛光盘转速设为固定值30 r/min,抛 光头转速设定为35~50 r/min,通过改变不同工艺 参数,对经过粗抛工艺后的碳化硅晶片进行了化学 机械抛光,并对抛光后的碳化硅晶片进行了测试分 析,抛光前碳化硅晶片表面粗糙度为3.2 nm,如图3 所示。
2.1 抛光液进给速率对晶片表面粗糙度的影响
研究抛光液进给速率对晶片表面粗糙度的影响规律,工艺参数为:抛光盘转速30 r/min,设定抛光 头转速50 r/min,抛光压力设定为200 N,抛光时长 设定为6 h,抛光液进给速率分别设定为1.8 mL/min、 2.6 mL/min、3.4 mL/min、4.2 mL/min,观察CMP后 晶片表面质量,在原子力显微镜(AFM)下观测到 的晶片表面粗糙度如图4所示。
在其他条件不变的情况下,随着抛光液进给速 率的增加,晶片的表面表面粗糙度随之减小,这是 由于抛光液较少时CMP中主要是机械抛光起作用, 随着抛光液增加,化学作用逐渐凸显,晶片表面质 量得到改善。
2.2 抛光头转速对晶片表面粗糙度的影响
设定抛光盘转速为30 r/min保持不变,设定抛光 压力为200 N,滴液速率为4.2 mL/min,抛光时长定 为10 h,改变抛光头转速,测量抛光后的晶片表面粗糙度,其结果如图5所示。
对测量结果进行了拟合,其拟合曲线如图6所 示,从图中可以看出,在保持其他条件不变的情况 下,随着抛光头转速的增加,碳化硅晶片表面粗糙 度逐渐减小,从0.12 nm下降到0.095 nm,这是由于 抛光头转速增加会加剧抛光液中的磨粒运动,从而 与晶片表面的接触更充分,但过快的转速容易导致 晶片出现崩边现象,当转速增加到50 r/min时,晶片 表面粗糙度可以达到0.1 nm以下,最低为0.096 nm。
2.3 抛光压力对晶片表面粗糙度的影响
同样将抛光盘转速固定为30 r/min,抛光头转速 定为50 r/min,滴液速率为4.2 mL/min,抛光时长定 为10 h,改变抛光头压力,对碳化硅晶片进行化学机 械抛光,测量抛光后晶片表面粗糙度,测量结果如图7所示。
抛光头压力对晶片表面粗糙度影响拟合曲线如 图8所示。随着抛光头压力逐渐增加,抛光后晶片 表面粗糙度也随之增加,由于随着压力的增加,晶 片与上下抛光盘之间的摩擦力会不断增大,抛光时 产生的损伤层也逐步增大,导致晶片表面粗糙度增 加,可得出,抛光压力保持在200 N时,抛光后晶片 表面质量最好,但过低的抛光压力会降低晶片的材 料去除效率,增加成本,因此将抛光压力定为200 N 最优。
2.4 抛光时长对晶片表面粗糙度的影响
将抛光盘转速固定在30 r/min,抛光头转速固定 为50 r/min,抛光压力保持200 N不变,滴液速率为 4.2 mL/min,研究了不同抛光时长对晶片表面粗糙度 的影响,经过CMP工艺后晶片表面粗糙度AFM图如 图9所示。
抛光时长对晶片表面粗糙度的拟合曲线如图10 所示。由图可见,当抛光时长为6 h时,晶片表面粗 糙度最大,随着抛光时间的加长,晶片表面粗糙度 明显下降,当抛光时长大于8 h时,表面粗糙度下降趋于稳定,化学作用和机械作用接近均衡,当抛光时 长增加到12 h时,晶片表面粗糙度最低达到0.083 nm。
2.5 晶片粘贴方式对晶片表面粗糙度的影响
除了上述抛光参数的研究之外,还分析了晶片 的吸附方式对其表面粗糙度的影响,固定其他条件 不变,即大盘转速30 r/min、抛光头转速50 r/min, 抛光压力200 N,滴液速率为4.2 mL/min,将碳化 硅晶片分别以水雾吸附及上蜡粘贴吸附的方式进行 CMP,抛光时长6.5 h,测得抛光后晶片表面粗糙度 AFM图如图11所示。
从图中可以看出,其他条件不变的情况下,上 蜡粘贴吸附进行抛光和水雾吸附进行抛光后碳化硅 晶片的粗糙度差别不大,说明两种吸附方式的不同 对晶片表面粗糙度影响不大,但水雾吸附方式所使 用的吸附垫成本较高,且寿命短,事后清理较为麻 烦,因此建议使用上蜡粘贴吸附方式。
本文中对碳化硅衬底晶片进行了超精密化学 抛光工艺,分析了抛光头转速、抛光压力及抛光时 长对碳化硅晶片表面粗糙度的影响,结果显示,抛光头转速的增加和抛光压力的减小有利于改善晶片 表面粗糙度,增大抛光时长可以进一步改善晶片质 量,最终确定了工艺中的最优参数,即:抛光液进 给速率为4.2 mL/min、抛光盘转速为30 r/min、抛光 头转速为50 r/min、抛光盘压力为200 N、抛光时长 为12 h时,碳化硅晶片表面质量最好,其粗糙度最好 可达0.083 nm。
来源:电子工艺技术第44卷第2期
作者:甘琨,刘彦利,史健玮,胡北辰
(中国电子科技集团公司第二研究所)
暂无评论哦,快来评论一下吧!
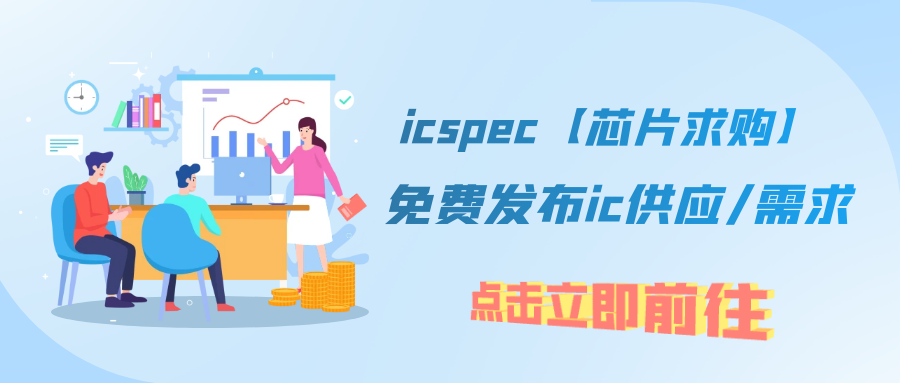
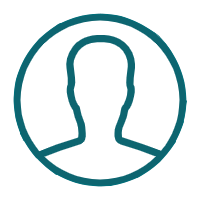