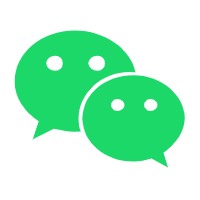
从这期开始,小编将为大家介绍从光刻胶的显影到最终检测所使用的基本方法。
显影
晶圆完成对准和曝光后,器件或电路的图案被以曝光和未曝光区域的形式记录在光刻胶上。通过对未聚合光刻胶的化学分解来使图案显影。显影技术被设计成使之把完全一样的掩膜版图案复制到光刻胶上。不良的显影工艺造成的问题是显影不充分,它会导致开孔的尺寸不正确,或使开孔的侧面内凹。在某些情况下,显影不够深而在开孔内留下一层光刻胶。第三个问题是过显影,这样会过多地从图形边缘或表面上去除光刻胶。要在保证高深宽比的塞孔的直径一致,和由于清洗深孔时液体不易进入而造成的清洗困难的情况下,保持具有良好形状的开孔是一个特殊的挑战。
负光刻胶和正光刻胶有不同的显影性质并要求不同的化学品和工艺。
正光刻胶显影
曝光后,预期的图形在正光刻胶中按照聚合光刻胶和未聚合的光刻胶的区域被编码。两个区域有不同的溶解率,约为1:4.这意味着在显影中总会从聚合的区域失去一些光刻胶。使用过度的显影液或显影时间过长可能导致光刻胶薄到不能接受的程度,其结果是可能导致在刻蚀中翘起或断裂。
有两种类型的化学显影液用于正光刻胶,碱-水溶液和非离子溶液。碱-水溶液可以是氢氧化钠或氢氧化钾。因为这两种溶液都含有可动的离子污染物,所以在制造敏感的电路时不能使用。大多数用正光刻胶的工艺线使用非离子的四甲基氢氧化铵溶液。
有时要添加表面活性剂来去除表面张力,使溶液更易亲和晶圆表面。正光刻胶的水溶性使它们在环保上比有机溶液的负光刻胶更具吸引力。
接着的显影步骤是为了停止显影过程和从晶圆表面去除显影液的冲洗。对正光刻胶冲洗用的是水,它带来的是更简单的处理和成本的降低,并有利于环境。
正光刻胶的显影工艺比负光刻胶更为敏感。影响结果的因素是软烘培时间和温度、曝光度、显影液浓度、时间、温度,以及显影方法。显影工艺参数由所有变量的测试来决定。
当使用正光刻胶时,显影和清洗工艺的严格控制是尺寸控制的关键。对正光刻胶显影液清洗的化学品是水。它的作用与负光刻胶清洗液相同,但是更便宜、使用更安全,更容易处理。
负光刻胶显影
在光刻胶上成功地使图案显影要依靠光刻胶地曝光机理。负光刻胶暴露在光线下,会有一个聚合地过程,它会阻止光刻胶在显影液中分解。在两个区域间由足够高的分解率,使得聚合的区域光刻胶几乎没有损失。大多数负光刻胶显影是用二甲苯作为显影液,它还被用做负光刻胶配方中的溶液。
显影完成前还要进行冲洗。对于负光刻胶。通常使用n-醋酸丁酯作为冲洗化学品,因为它既不会使光刻胶膨胀也不会使之收缩,从而不会导致图案尺寸的改变。对具有台阶图案的晶圆,可能使用一种性质较温和的Stoddand溶剂。
湿法显影
有几个方法用于光刻胶显影。方法的选择依据包括光刻胶极性、特征图形尺寸、缺陷密度的考虑、要刻蚀层的厚度以及产能。
沉浸式显影:
沉浸式使最古老的显影方法。在这种最简单的方式中,在耐化学腐蚀的传输器中的晶圆被放进盛有显影液的池中一定时间,然后再被放入加有化学冲洗液的池中进行冲洗。这种简单的湿法过程的问题有:
液体的表面张力组织了化学液体进入微小开孔区。
部分溶解的光刻胶块会粘在晶圆表面。
随着几百片晶圆处理过后化学液池会被污染。
当晶圆被提出化学液面时会被污染。
显影液随着使用会被稀释。
为了消除1、2和3的问题需要进场更换化学液从而增加了成本。
室温的波动改变溶液的显影率。
晶圆必须迅速送到下一步进行干燥,这就增加了一个工艺步骤。
喷雾式显影:
最受欢饮的化学显影方法就是喷雾式的。事实上,通常有很多原因使喷雾式工艺对于任何湿法工艺来讲比沉浸式工艺更受欢迎。例如,用喷雾式系统可大大降低化学品的使用。工艺的提高包括由于因喷雾压力的机械动作而限定光刻胶边缘和去除部分光刻胶块而带来较好的图案清晰度。因为每个晶圆都是用新的化学显影液,所以喷雾式系统总比沉浸系统清洁。
混凝式显影:
喷雾式显影因其均匀性和产能高而非常有吸引力。混凝显影是用以获得正光刻胶喷雾工艺优点的一种工艺的变化。该系统使用一个标准的单晶圆喷射装置。正常的喷雾式显影和混凝显影的区别是用于晶圆的显影化学品的不同。工艺开始时,在静止的晶圆表面上覆盖一层显影液。表面张力使显影液在晶圆表面上不会流散到晶圆外。
等离子体去除浮渣:
不完全显影造成的一个特殊困难称为浮渣。浮渣可以是留在晶圆表面上的未溶解的光刻胶块或是干燥后的显影液。膜很薄并很难直观检验。为了解决这个问题,在微米和微米以下的甚大规模集成电路生产线中,在化学显影后用氧离子体来去除这种薄膜。
干法显影
液体工艺的消除一直是一个长期目标。它们难以集成到自动化生产线,并且化学品的采购、储存、控制和处理费用昂贵。取代液体化学显影液的途径是使用等离子体刻蚀工艺。干法等离子体刻蚀对于刻蚀晶圆表面层已经是很完善的工艺了。在等离子体刻蚀中,离子有等离子体场得到能量,以化学形式分解暴露的晶圆表面层。干法光刻胶显影要求光刻胶化学物的曝光或未曝光的部分二者之一易于被氧等离子体去除。换句话说,巴巴图案的部分从晶圆表面氧化掉。一种称为DESIRE的干法显影工艺得以实现,它采用甲基烷烃和氧等离子体。
硬烘培
硬烘培是在掩模工艺中的第二个热处理操作。它的作用实质上和软烘培是一样的,通过溶液的蒸发来固化光刻胶。然而,对于硬烘培,其唯一的目标是使光刻胶和晶圆表面有良好的黏结,这个步骤有时称为刻蚀前烘培。
硬烘培的方法
硬烘培是在设备和方法上与软烘培相似。对流炉、在线及手动热板、红外线隧道炉、移动带传导炉和真空炉都用于硬烘培。对于自动生产线,轨道系统受到青睐。
硬烘培工艺
硬烘培的时间和温度的选取与在软烘培工艺中是相同的。起始点是由光刻胶制造商推荐的工艺。之后,工艺被精确调整,以达到黏结和尺寸控制的要求。一般使用对流炉的硬烘培的温度是从130℃~200℃进行30分钟。对于其他方法,时间和温度有所不同。设定最低温度使光刻胶图案边缘和晶圆表面达到良好黏结。热烘培增强黏结的机理是脱水和聚合。加热使水分脱离光刻胶,同时使之进一步聚合,从而增强了其耐刻蚀性。
硬烘培温度的上限以光刻胶流动点而定。光刻胶有像塑料的性质,当加热时会变软并可流动。当光刻胶流动时,图案尺寸便会改变。当在显微镜下观察光刻胶流动时,将会明显增厚光刻胶边缘。极度的流动会在沿图案边缘处显示出边缘线。边缘线是光刻胶流动后在光刻胶中留下的斜坡而形成的光学作用。
硬烘培是紧跟在显影后或马上再开始刻蚀前来进行的。在大多数生产情况中,硬烘培是由和显影机并排在一起的隧道炉完成的。当使用此种操作规程时,把晶圆存放在氮气中或是立即完成检验步骤以防止水分重新被吸收到光刻胶中,这一点非常重要。
工艺过程中的一个目标是有尽可能多的共同工艺。对于硬烘培工艺来说,由于各种晶圆表面的不同黏结性质有时会给工艺带来困难。更加困难的表面,如铝和掺杂磷的氧化物,有时要经高温硬烘培或在即将要刻蚀之前对其在对流炉中进行二次硬烘培。
显影检验
在显影和烘培之后就要完成光刻掩模工艺的第一次质检。恰当的说,应该叫显影检验,简称DI。检验的目的是区分那些通过最终掩模检验可能性很小的晶圆;提供工艺性能和工艺控制数据;以及分拣出需要返工的晶圆。
这时的检验良品率,也就是通过第一次质检的晶圆数量,不会计入最终的工艺良品率的计算。但是两个主要原因使之成为很受关注的良品率。光刻掩膜工艺对于电路性能的关键性已经着重强调。在显影检验工艺,工艺师有第一个判断工艺性能的机会。显影检验步骤的第二个重要性与在检验时做的两种拒收有关。首先,一部分晶圆是由于在上一步骤中遗留下来问题而要停止工艺处理。这些晶圆在显影检验时会被拒绝接收并丢弃。其他在光刻胶上有光刻图案问题的晶圆可以被通过去掉光刻胶的办法重新进行工艺处理,因为在晶圆上还没有永久改变,所以这是整个制造工艺中发生错误后能够返工的几个步骤之一。
晶圆被送回掩模工艺称为返工或重做。工艺师的目标是保持尽可能低地返工率,应少于10%,而5%是一个最受欢迎的返工水平。经验显示经过光刻返工地晶圆在最终工艺完成时有较低的分选良品率。返工会引起黏结问题,并且再次传输操作会导致晶圆污染和破坏。如果太多地晶圆返工会使整个分选良品率受到严重影响,并且生产线将被堵塞。
保持低返工率地第二个原因与在及逆行返工晶圆处理时要求另外的计算和标识有关。显影检验良品率和返工率随掩模水平而变。总体上,在掩模次序中的第一级有较宽的特征图形尺寸、较平的表面和较低的密度,所有这些会使掩模良品率更高。在晶圆到了关键的接触和连线步骤时,返工率呈上升趋势。
显影检验的方法
自动检验:随着芯片尺寸的增加和元件尺寸的减少,工艺变得更加繁多并精细,较老的和相对慢的人工检验的效率液到了极限。可探测表面和图案失真的自动检验系统称为在线和非在线检验的选择。自动检验系统提供了更多数据,反过来,这又使工艺师能够刻画出工艺特色并对工艺加以控制。
人工检验:第一步是用眼睛直接检验晶圆表面。用这种方法可以非常有效的检查出膜厚的不均匀、粗显影问题、划伤及污染,特别是污渍。
在显影检验阶段拒收的原因
有很多原因可使晶圆在显影检验时被拒收。一般地,要找的仅是那些在当前光刻掩膜步骤增加的缺陷。每一片晶圆都会带有一些缺陷问题,并且晶圆达到当前步骤时有可接受的质量,在这一原理下,从上一步留下的缺陷一般会被忽略掉。如果一片晶圆有严重的问题而在上一步未被发现,就会从本批中拿掉。
刻蚀
在完成显影检验步骤后,掩膜版的图形就被固定在光刻胶膜上并准备刻蚀。在刻蚀后图形就会被永久的转移到晶圆的表面。刻蚀就是通过光刻胶暴露区域来去掉晶圆最表层的工艺。
刻蚀工艺主要有两大类:湿法和干法刻蚀。两种方法的主要目标是将光刻掩膜版上的图形精确的转移到晶圆的表面。其他刻蚀工艺地目标包括一致性、边缘轮廓控制、选择性、洁净度和拥有成本最低化。
湿法刻蚀
历史上的刻蚀方法一直使用液体刻蚀剂沉浸技术。规程类似于氧化前清洁-冲洗-干燥工艺中去除残留的酸,再送到最终清洗台以冲洗和甩干。湿法刻蚀用于特征图形尺寸大于3um的产品。低于此水平时,由于控制和精度的需要就应使用干法刻蚀了。
刻蚀一致性和工艺控制由附加的加热器和搅动设备来提高,例如,搅拌器或带有超声波和兆频超声波的槽。
被选择的刻蚀液要有可均匀地去除晶圆表层又不伤及下一层材料的能力。
刻蚀时间的变化性是一个工艺参数它受料盒和晶圆再槽中到达我呢度平衡过程中温度变化的影响和在晶圆被送入冲洗槽过程中持续刻蚀的影响。一般地,工艺被设置在最短的时间并保持在均匀刻蚀和高生产力。最大时间受限于光刻胶在晶圆表面的黏结时间。
刻蚀的目的和问题
图形复制的精度依靠几个工艺参数。它们包括:不完全刻蚀、过刻蚀、钻蚀、选择比和侧边的各向异性/各向同性刻蚀。
不完全刻蚀
不完全刻蚀是指表面层还留在图形孔中或表面上的情况。不完全刻蚀的原因是可是时间太短,出现可减慢刻蚀时间的表面层,或是一个薄层不均匀的表层也可导致在厚的部分产生不完全刻蚀。如果使用化学湿法刻蚀,过低的温度或弱的刻蚀液会导致不完全刻蚀。如果是干法等离子刻蚀,不正确的混合气体或不当的系统运行可导致相同的影响。
过刻蚀和钻蚀
与不完全刻蚀相反的是过刻蚀。在任何的刻蚀工艺中,总会有一定程度的、有计划的过刻蚀,以便允许表面层厚度的变化。有计划的过刻蚀还可用以突破最外表层的缓慢刻蚀层。
理想的刻蚀应在表面中形成垂直的侧边。产生这种理想结果的刻蚀技术称为各向异性刻蚀。然而,刻蚀剂会从各个方向去掉材料,这种现象称为各向同性。在从最外表层刻蚀到表层底部的过程中刻蚀也会在最外表面进行。结果会在侧边形成一个斜面。这种作用因在光刻胶边缘下被刻蚀,所以被称为钻蚀。一个持续的刻蚀目标是把钻蚀水平控制在一个可接受的范围内。电路版图的设计者在计划电路时会把钻蚀考虑在内。相邻的图形必须要分开一定的距离以防止短路。在图形设计时必须计算钻蚀量。各向异性刻蚀可用等离子体刻蚀的方法来得到,它用于刻蚀高级电路时受到青睐。钻蚀的减少可允许制作更密的电路。
当刻蚀时间过长,刻蚀温度太高,或是刻蚀剂混合物太强便会发生严重的钻蚀。当光刻胶和晶圆表面黏结力较弱时也会发生钻蚀。这是一个持续令人单行的问题。干燥脱水、底胶、软烘培和硬烘培的目的就是用来防止这种问题的。在刻蚀开孔的边缘光刻胶黏结附力的失效会导致严重的钻蚀。如果黏结力非常弱,光刻胶会翘起而导致极为严重的钻蚀。
选择比
刻蚀工序的另一个目标是保护被刻蚀层下的表面。如果晶圆的下层表面被部分刻蚀掉,则器件的物理尺寸和电性能会发生改变。与保护表面相关的刻蚀工艺的性质是选择比。它由被刻蚀层的刻蚀速率与被刻蚀层下面表层的刻蚀速率的比来表示。以不同的刻蚀方法氧化硅/硅的选择比为20~40.高选择性意味着下表层很少或没有被刻蚀。在刻蚀深宽比大于3:1的小接触孔时,良好的选择性也会成为一个问题。选择比还适用于光刻胶去除。这在干法刻蚀中考虑较多。在表层被刻蚀的同时,一些光刻胶也会被同时去除。选择比必须足够高,以保证刻蚀完成前光刻胶不会在被刻蚀层之前被去除掉。
湿法喷射刻蚀
湿法喷射刻蚀相对沉浸刻蚀有几个优点。其主要优点是喷射的机械压力而增加的精确度。湿法刻蚀可以将来自刻蚀剂的污染讲到最低程度。从工艺控制的观点来看,喷射刻蚀因刻蚀剂可被水冲洗从而可以及时的从表面去掉而更加可控。单晶圆旋转喷射系统有显著的工艺一致性的优点。
喷射刻蚀的缺点时设备系统的成本,对于压力系统中有毒刻蚀剂的安全考虑以及用于防止机器老化的防刻蚀材料的要求方面。其优点为:喷射刻蚀系统通常是封闭的,这增加了操作人员的安全性。
对于小特征尺寸和/或更大直径晶圆,批浸没式刻蚀虽然有生产效率高的优点,也不满足均匀性的要求。具有机械手自动装卸系统的单片晶圆模块喷雾设备克服了批浸没式刻蚀的局限性。它们提供了需要的化学组分的控制、定时和刻蚀的均匀性。
暂无评论哦,快来评论一下吧!
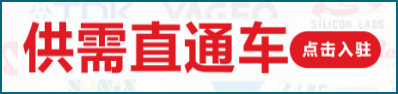